.jpg)
In modern pharmaceuticals, dry powder injection plays a vital role in the treatment of various diseases. These sterile formulations are widely used in healthcare settings due to their stability, extended shelf life, and ability to effectively deliver potent drugs. Injectable powder formulations are crucial for the treatment of bacterial infections, chronic diseases, and emergency medical conditions.
This article provides an in-depth analysis of injectable dry powder, its uses, advantages, and the importance of injectable powder manufacturing in the pharmaceutical industry.
What is Dry Powder Injection?
Dry powder for injection refers to the sterile, lyophilized, or powdered form of a drug that requires reconstitution with a suitable solvent before administration. Unlike liquid injections, these formulations are highly stable, making them ideal for long-term storage. Powder injections are typically used for drugs that are unstable in liquid form. Injectable powders must be reconstituted using sterile water, saline, or other suitable diluents before administering via intravenous (IV), intramuscular (IM), or subcutaneous (SC) routes.
Uses of Dry Powder Injection
The pharmaceutical industry widely uses dry powders for injection in various therapeutic areas. Some common applications include:
1. Antibiotics and Antimicrobials
- Cefazolin, cefepime, cefuroxime, and ceftriaxone are common injectable dry powder antibiotics used to treat serious bacterial infections.
- Dry powder injection formulations ensure stability and effectiveness against resistant bacteria.
2. Pain Management and Anti-Inflammatory Drugs
-
Diclofenac sodium, aceclofenac and betamethasone sodium are usually available in powder form for injection to reduce inflammation and pain.
3. Proton Pump Inhibitors (PPIs)
-
Pantoprazole and Rabeprazole in the form of injectable powder are used to treat acid-related disorders such as GERD and peptic ulcers.
4. Corticosteroids and Hormonal Treatments
-
Dexamethasone and nandrolone decanoate are available as dry powder for injection to manage allergic reactions, inflammation and muscle wasting conditions.
5. Anesthetics and Sedatives
-
Lorazepam and ondansetron in injectable powder form are used for pre-anesthesia and nausea control, respectively.
6. Veterinary Applications
-
Veterinary dry powder injectable formulations are used to treat infections and other conditions in animals, ensuring effective treatment and rapid recovery.
Advantages of Dry Powder Injection
1. Extended Shelf Life
-
Dry powder injection formulations can have longer shelf life than liquid injections due to the absence of water, reducing the risk of microbial contamination.
2. Enhanced Stability
-
Some medications disintegrate rapidly in liquid form, making powders for injection a preferred option for long-term storage and stability.
3. Higher Drug Potency
-
Injectable powder manufacturing ensures that drugs retain their full potency until the time of use, as reconstitution is done just before administration.
4. Easy Storage and Transport
-
Since dry powder for injection does not require refrigeration, it is easy to store and transport, making it ideal for remote areas and emergency use.
5. Reduced Risk of Preservatives and Contaminants
-
Unlike liquid injections, powder injection formulations do not require preservatives, reducing the risk of adverse reactions caused by additives.
The Role of Injection Powder Manufacturing
Manufacturing Process
Strict quality control measures are followed in the production of dry powder injections, ensuring safety and efficacy. Common steps include:
- Raw Material Selection: High-quality active pharmaceutical ingredients (APIs) are selected.
- Sterilization and Lyophilization: Injectable powders are sterilized and freeze-dried to ensure stability.
- Filling and Sealing: Injectable powders are filled into vials under aseptic conditions and sealed to prevent contamination.
- Packaging and Distribution: The final product undergoes rigorous testing before being packaged and distributed globally.
Quality Control and Regulatory Compliance
Pharmaceutical companies follow good manufacturing practices (GMP) and comply with international regulatory standards such as:
-
U.S. FDA (Food and Drug Administration)
-
WHO (World Health Organization)
-
EU GMP (European Good Manufacturing Practice)
Ensuring high-quality injection powder manufacturing is critical to patient safety and drug efficacy.
Challenges in Dry Powder Injection Production
Despite its advantages, Dry Powder for Injection manufacturing faces certain challenges, including:
- Strict aseptic conditions: Maintaining sterility is complex and requires advanced infrastructure.
- Reconstitution issues: Incorrect dilution can lead to ineffective drug action or adverse reactions.
- Cost of production: The injectable powder manufacturing process is more expensive than liquid formulations due to strict quality control measures.
Future Trends in Dry Powder Injection
1. Innovative Drug Delivery Systems
-
Nanotechnology and Dry Powder for Injection advancements are improving bioavailability and efficacy.
2. Expansion in Biologics and Vaccines
-
More biologic drugs and vaccines are being developed in Powder Injection form to enhance stability and storage.
3. Automation in Manufacturing
-
AI and robotic technologies are enhancing precision in Injection Powder Manufacturing, reducing errors and contamination risks.
Conclusion
Dry powder injections have transformed modern medicine by providing a stable, effective, and long-lasting solution for drug administration. From antibiotics to pain management and veterinary treatments, injectable dry powder offers many advantages over liquid injectables. With continued advancements in injectable powder manufacturing, the future of dry powder for injection looks promising, ensuring better healthcare solutions around the world.
By adhering to stringent regulatory standards and using cutting-edge technology, drug manufacturers can enhance the quality, safety, and efficacy of powder formulations for injection, contributing to better patient outcomes and global healthcare improvements.
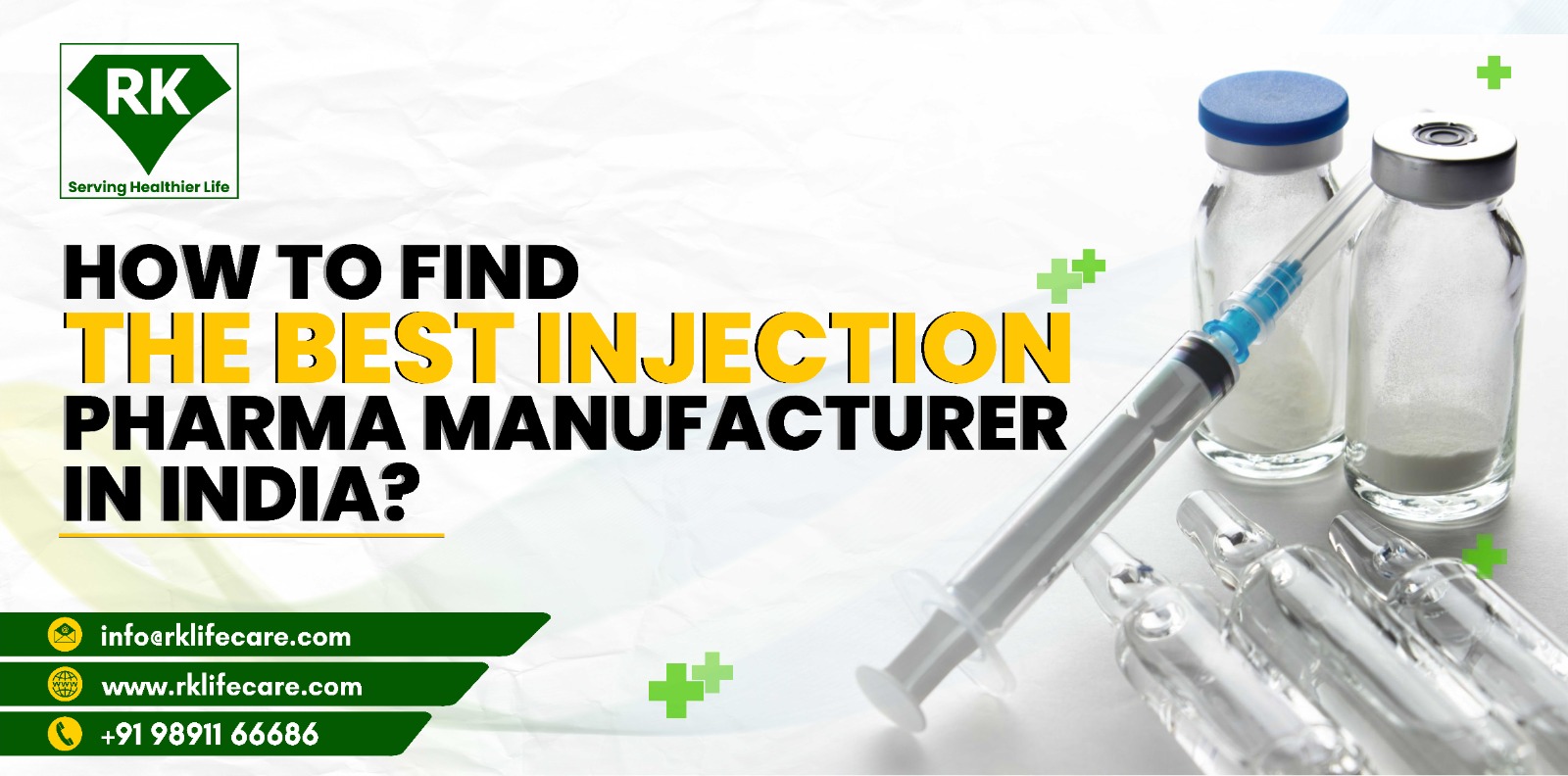
22 Apr 2025
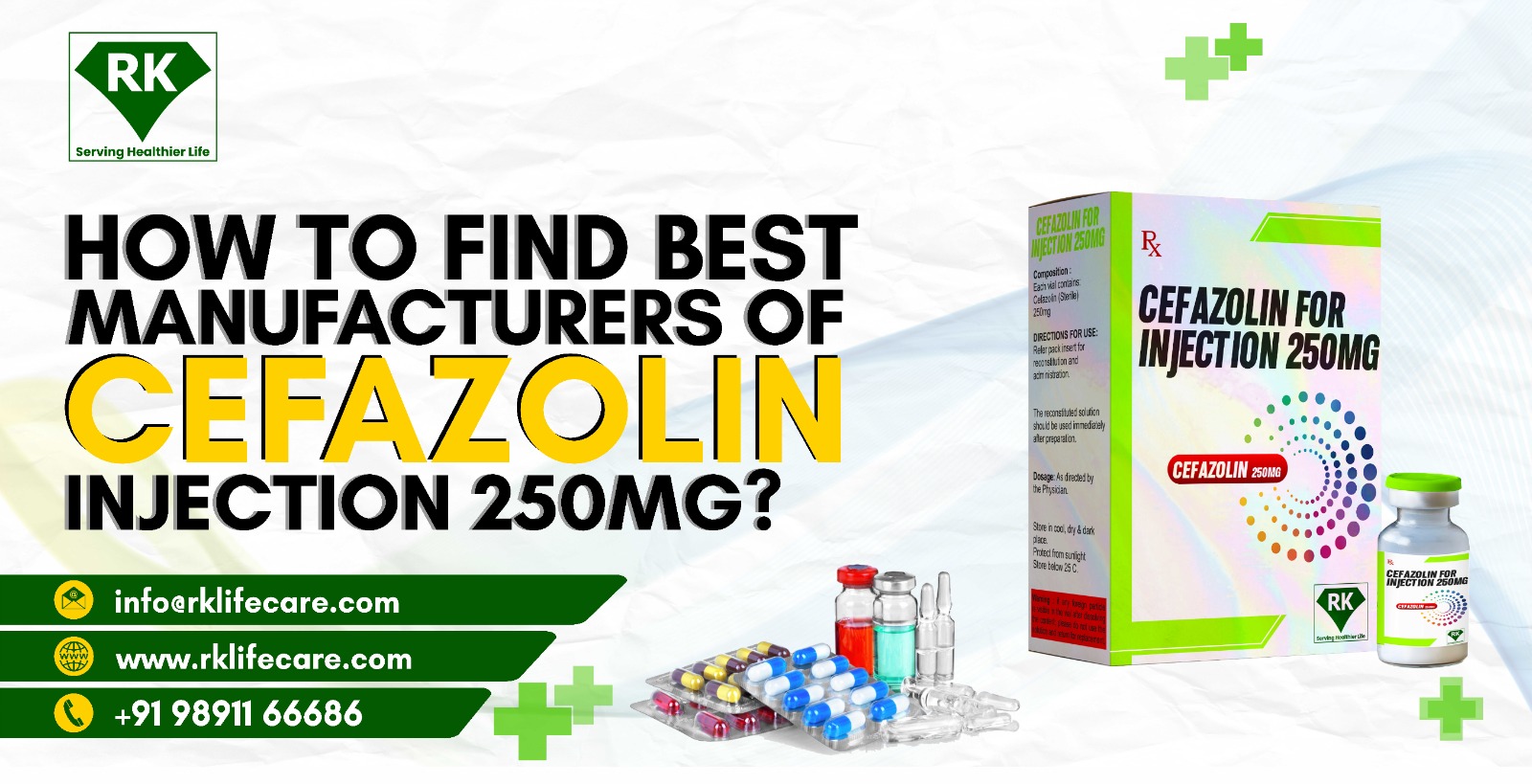
18 Apr 2025
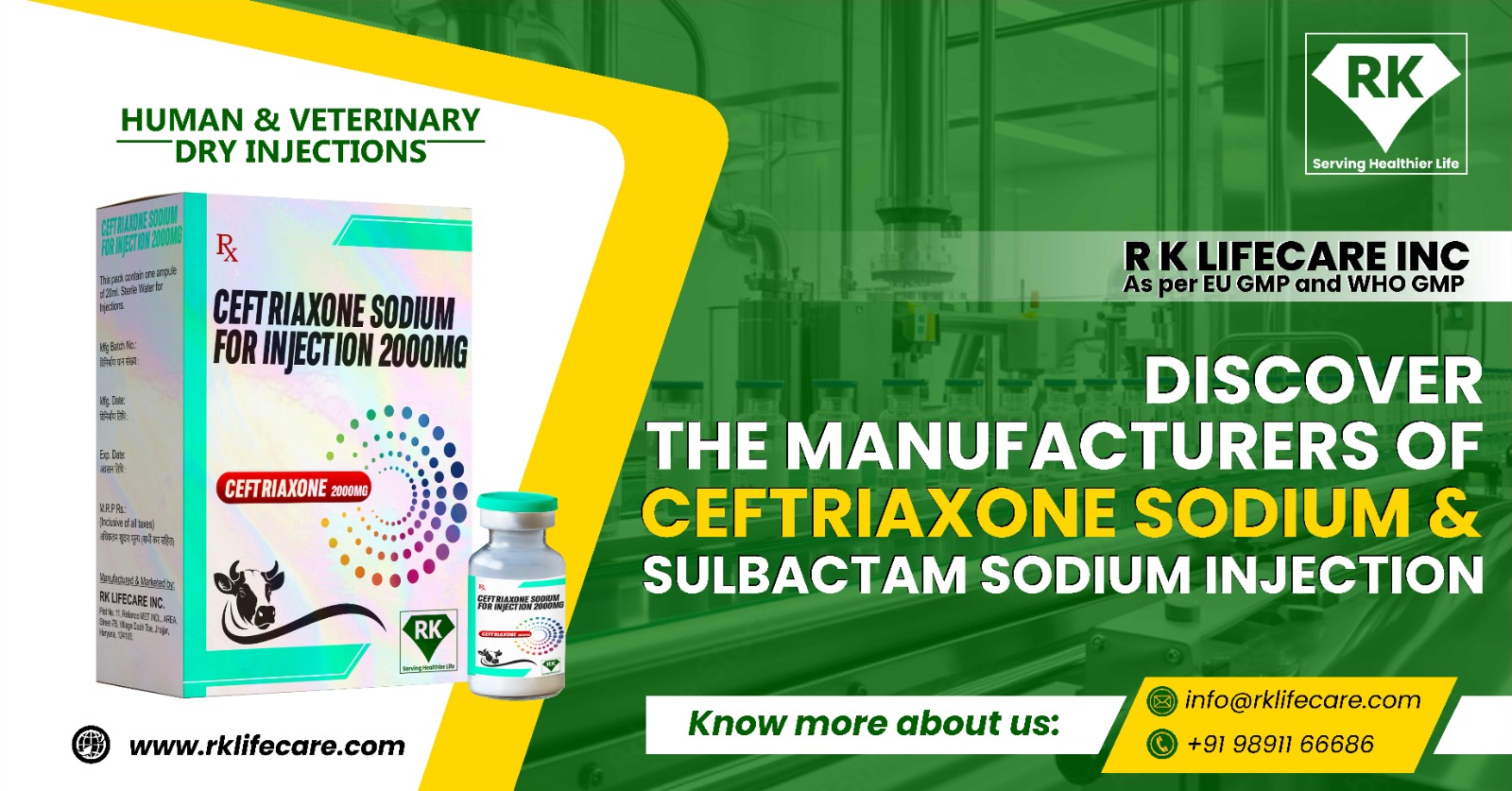
16 Apr 2025
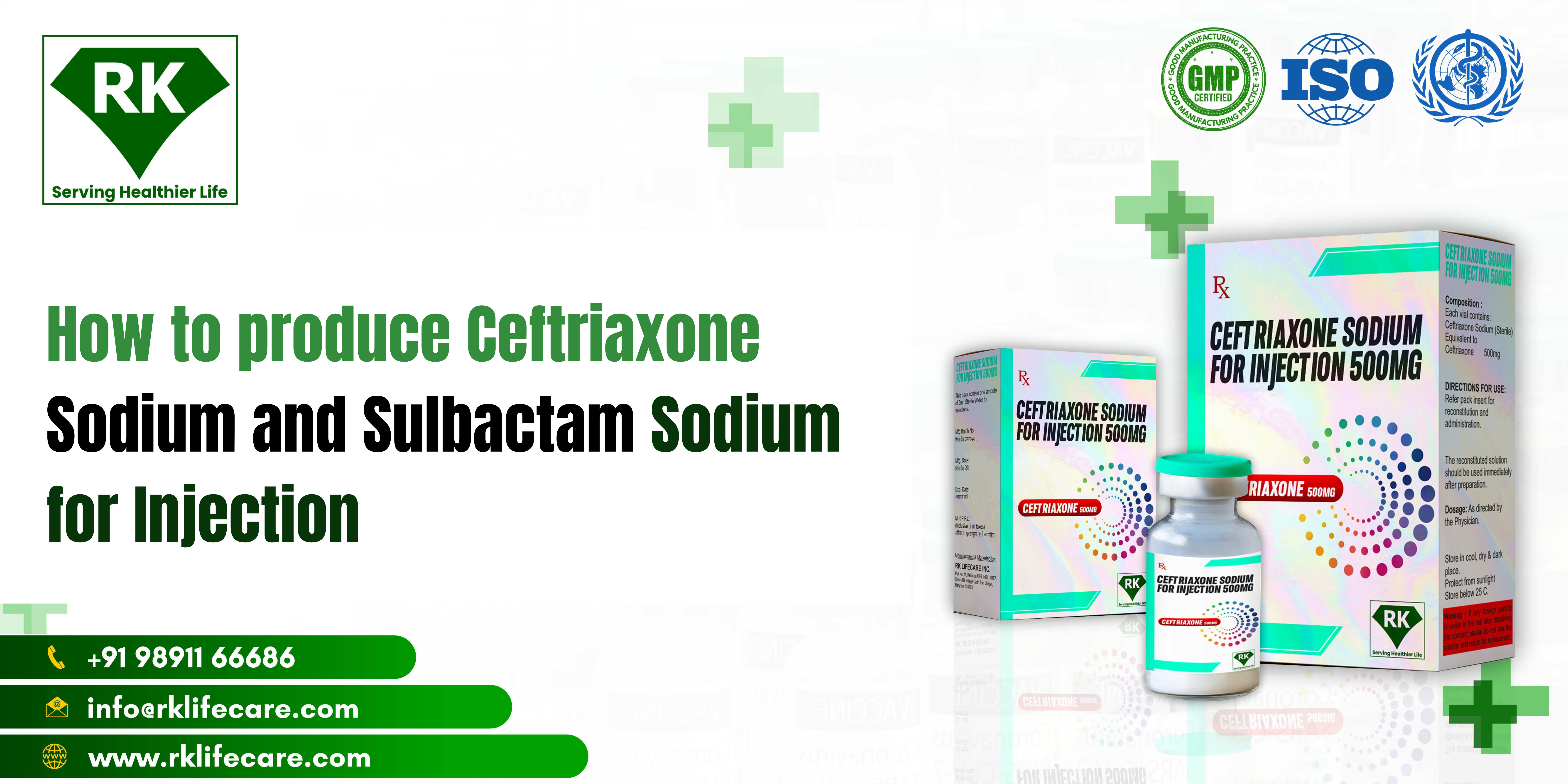
12 Apr 2025
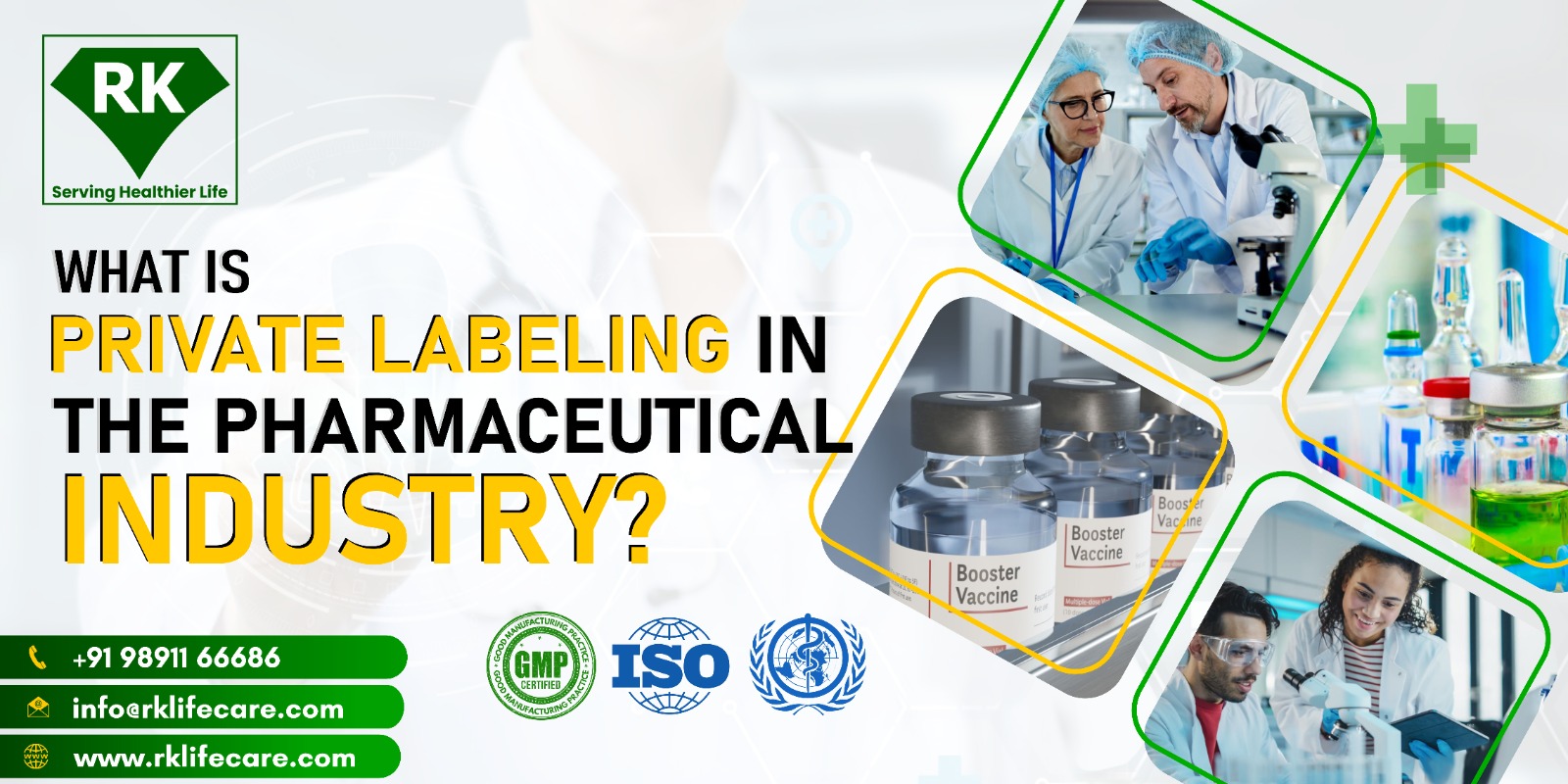
02 Apr 2025
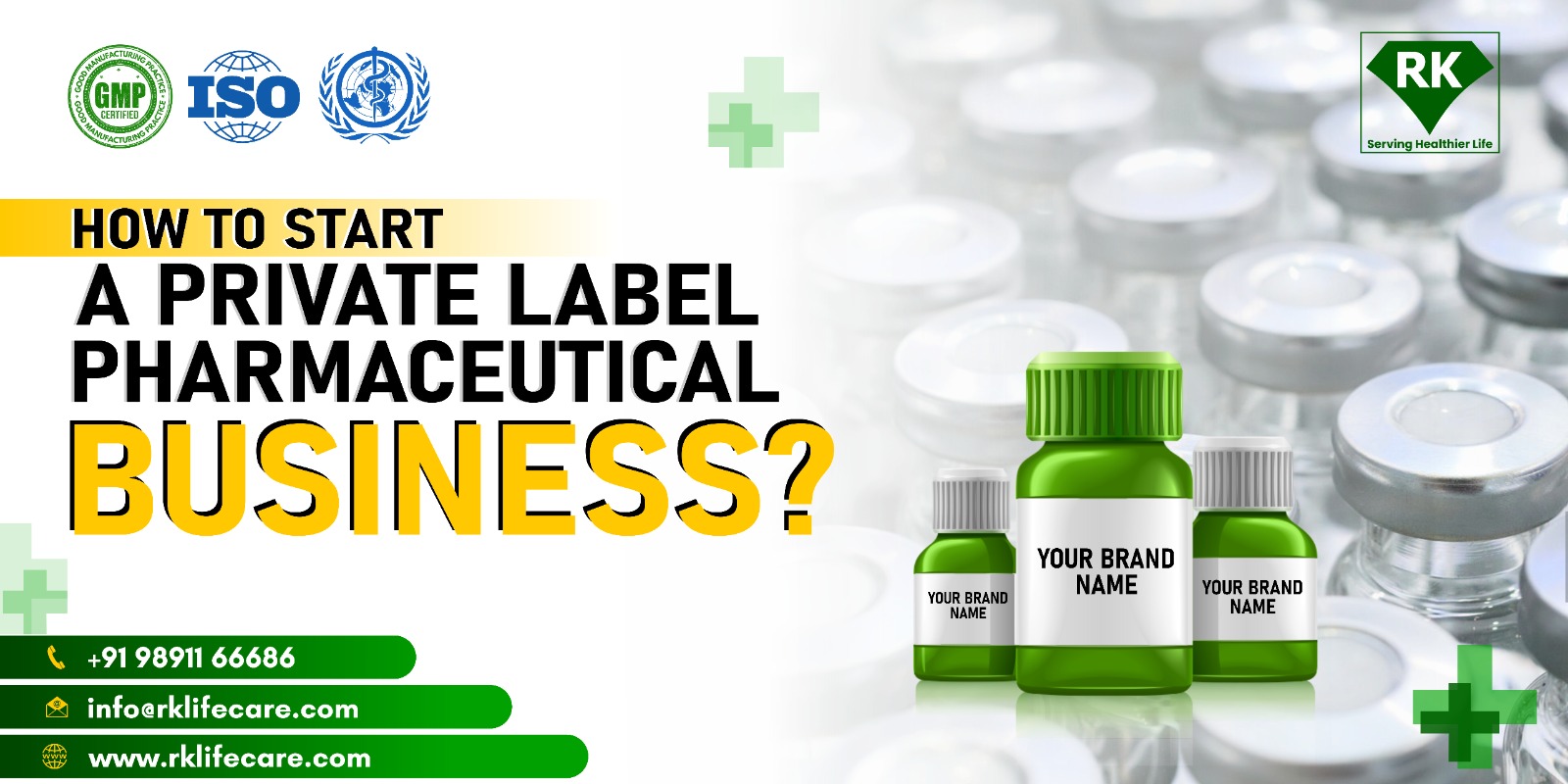
28 Mar 2025
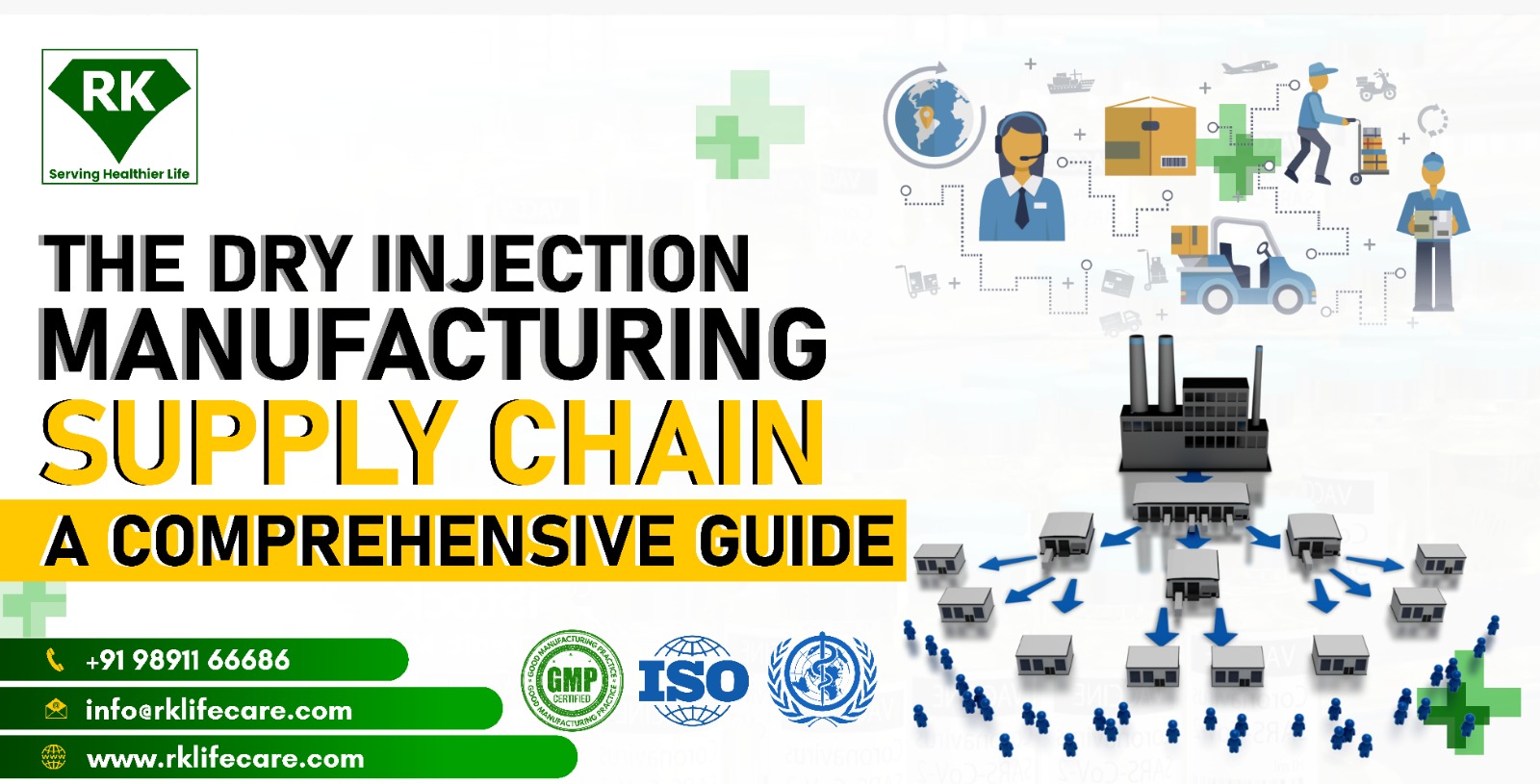
26 Mar 2025
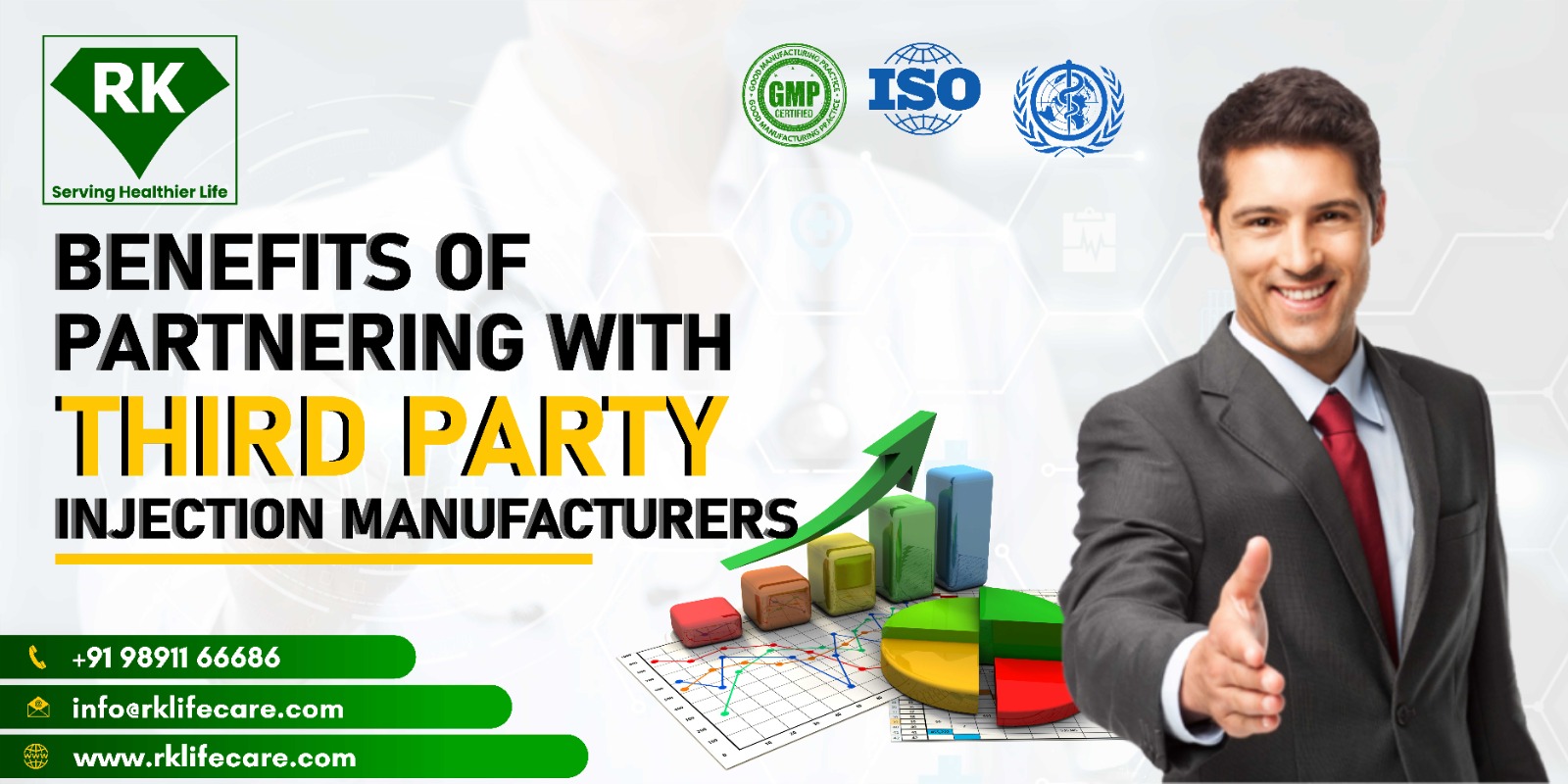
24 Mar 2025
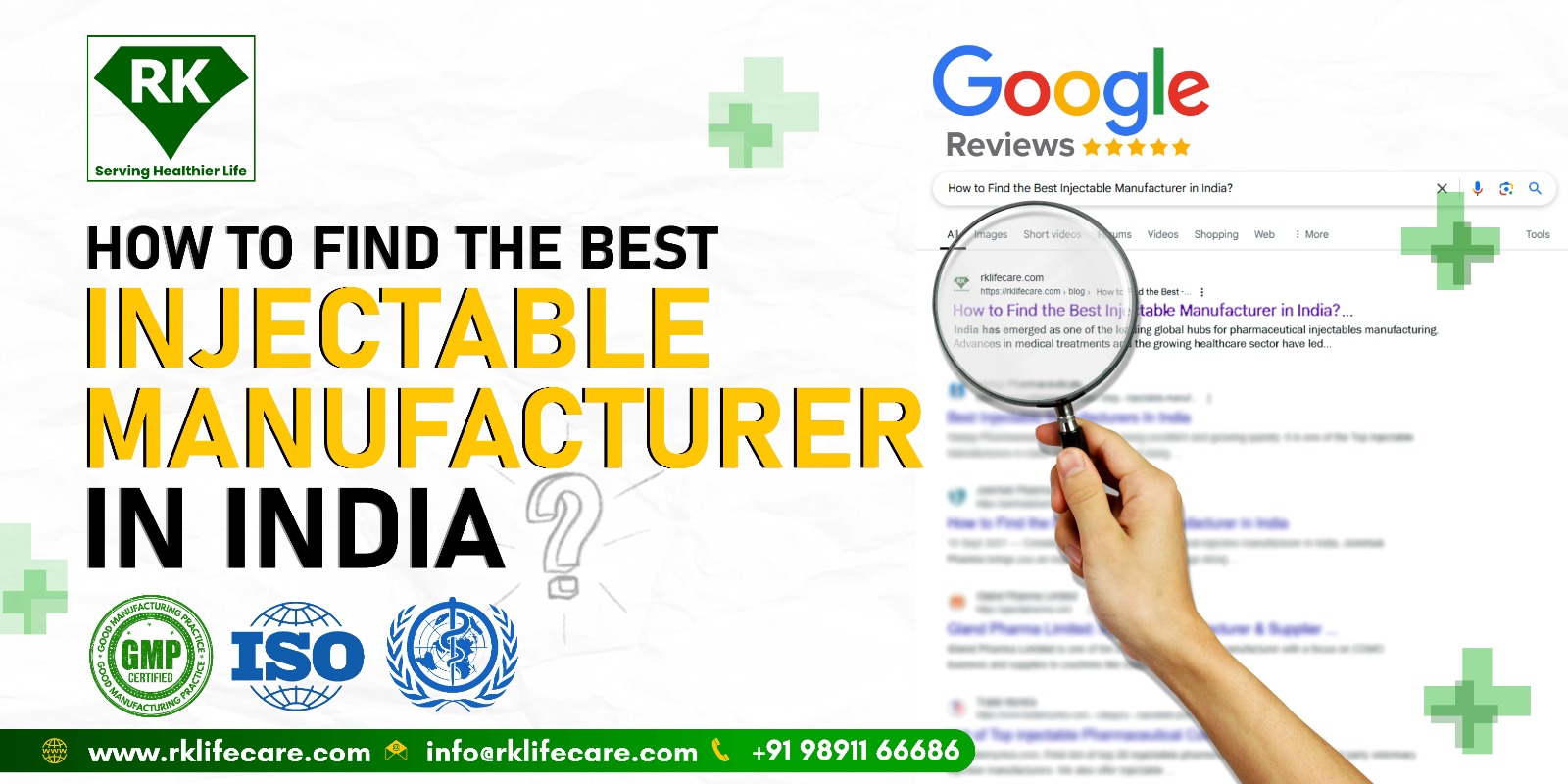
18 Mar 2025
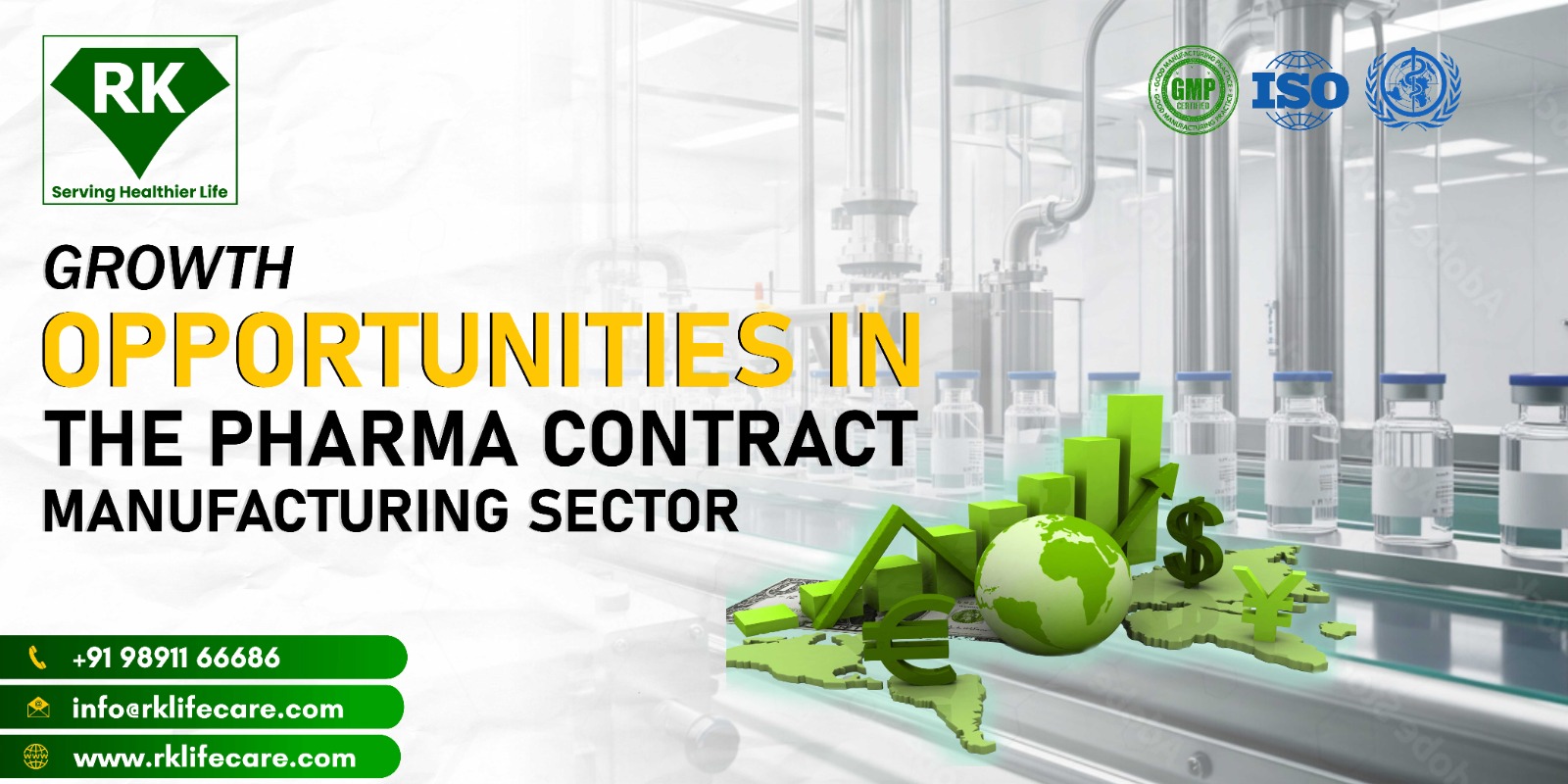
12 Mar 2025
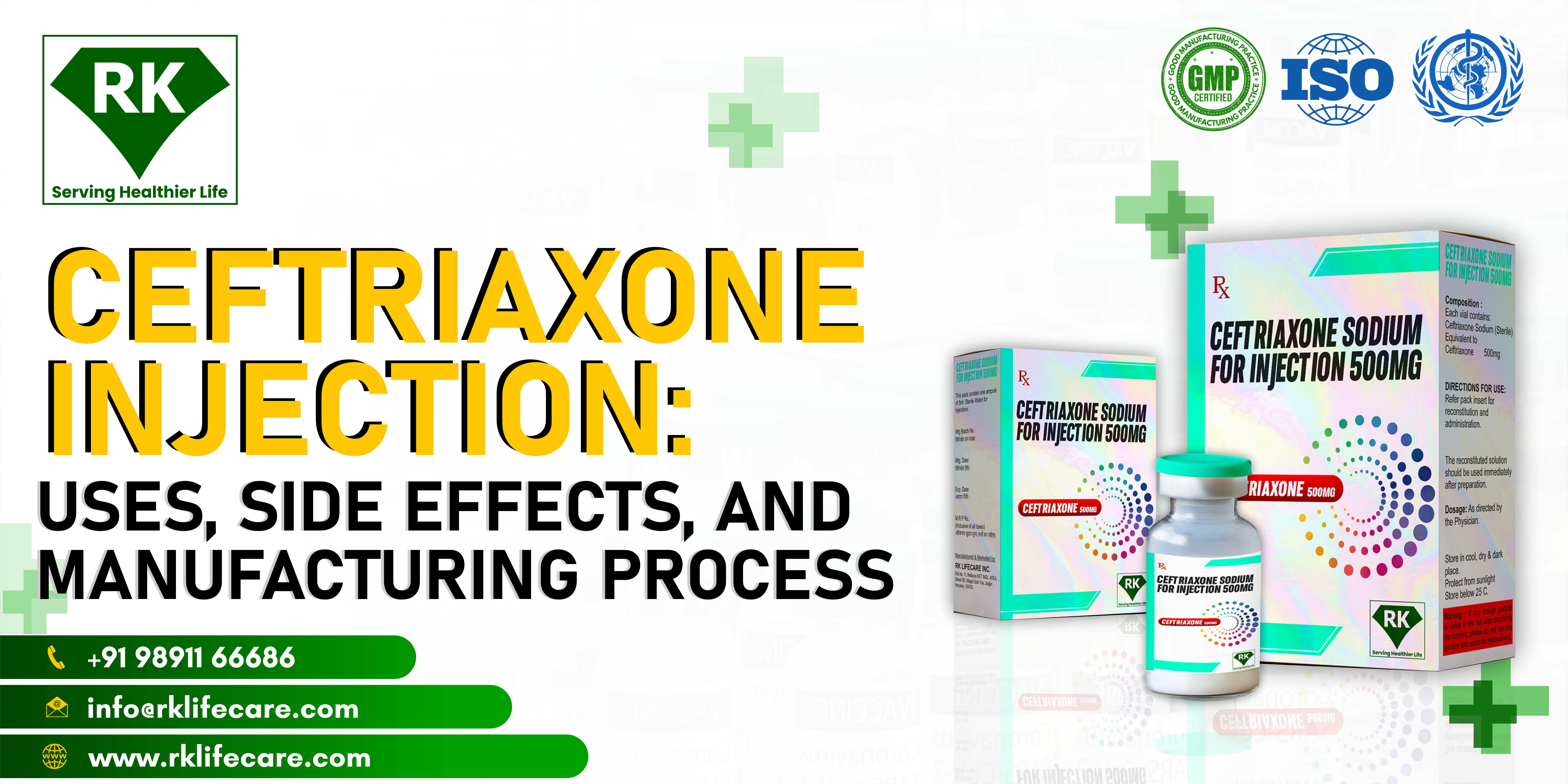
08 Mar 2025
.jpg)
28 Feb 2025
.jpg)
27 Feb 2025
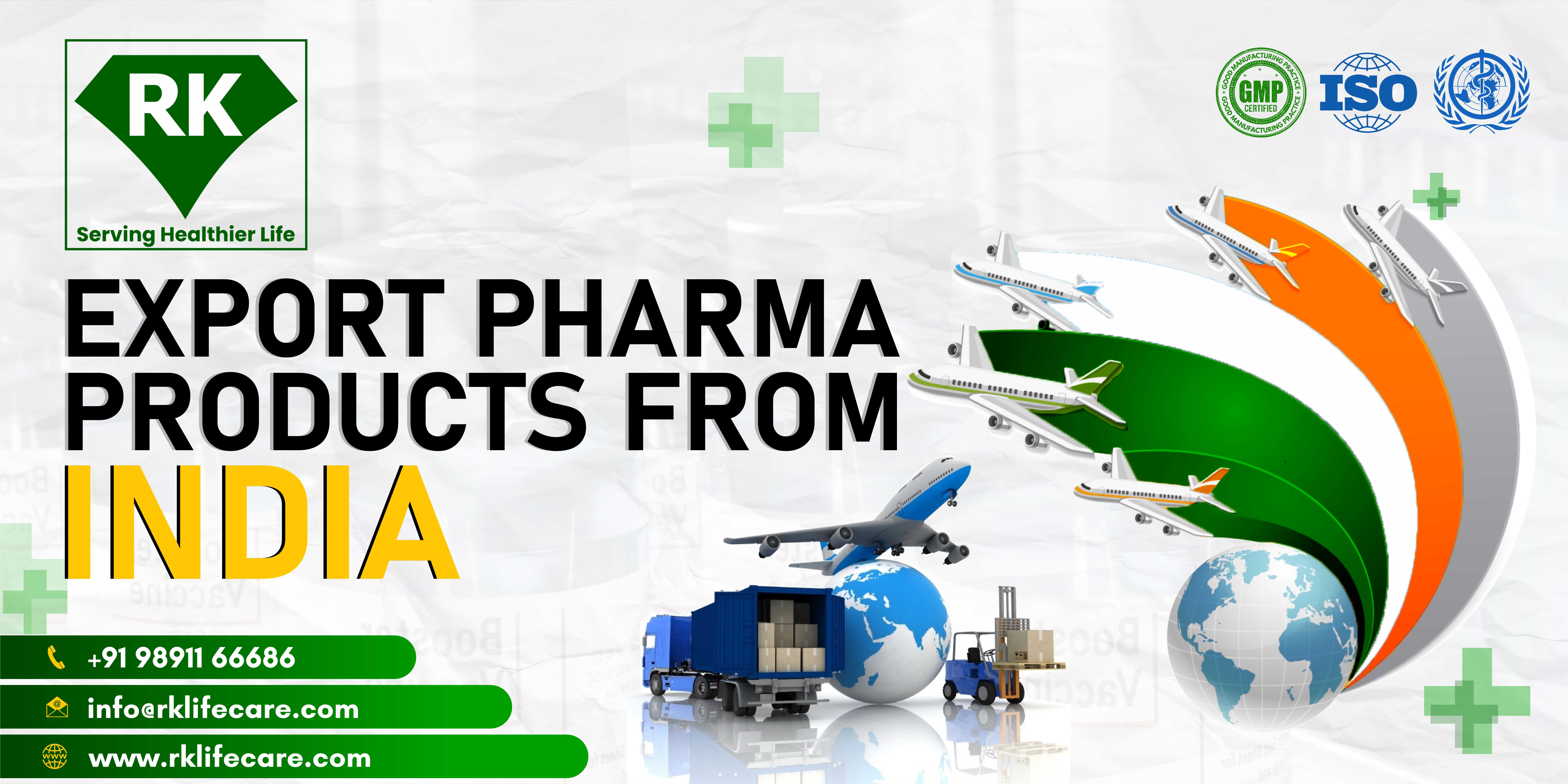
26 Feb 2025
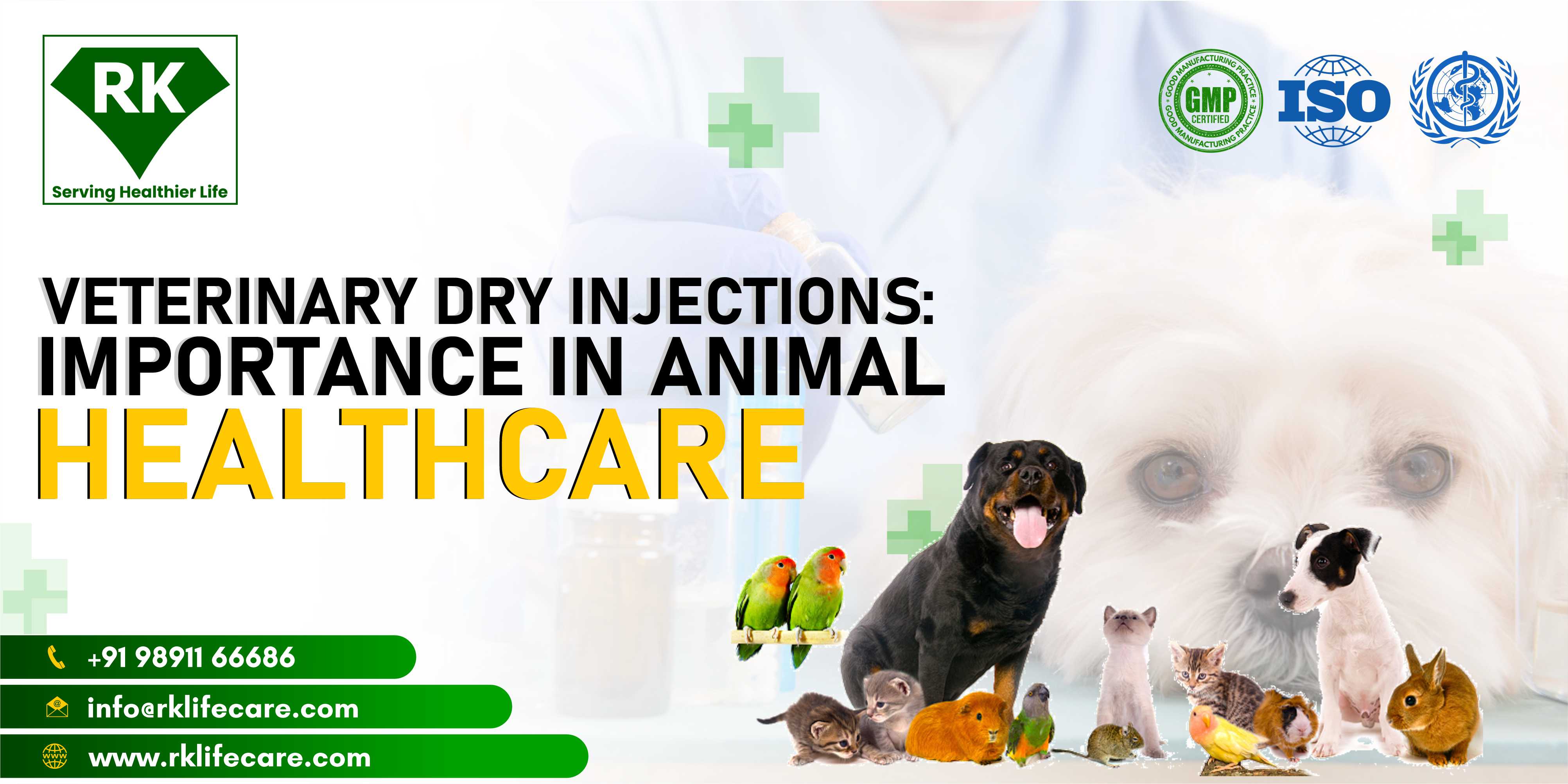
25 Feb 2025
.jpg)
24 Feb 2025
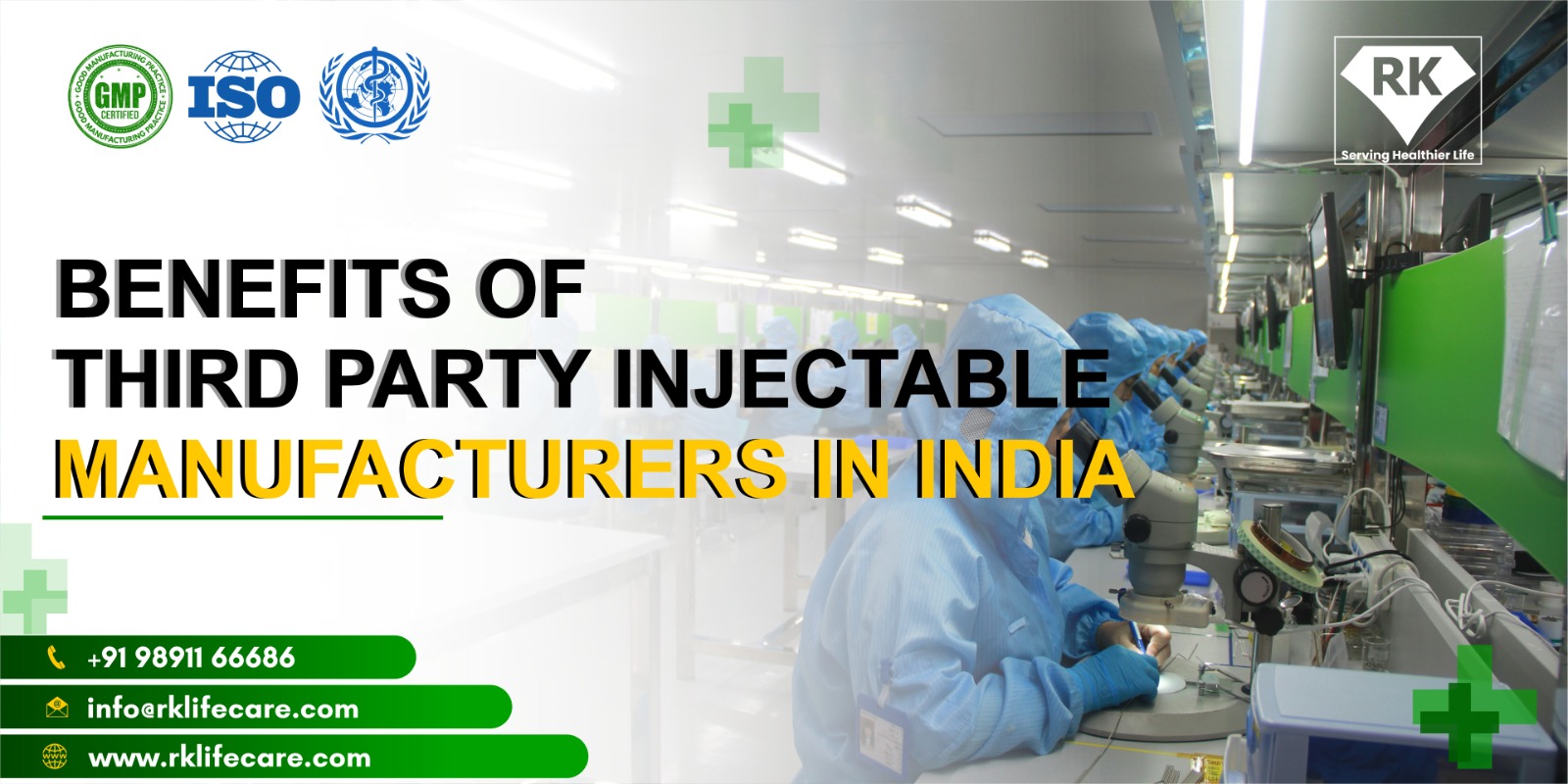
22 Feb 2025
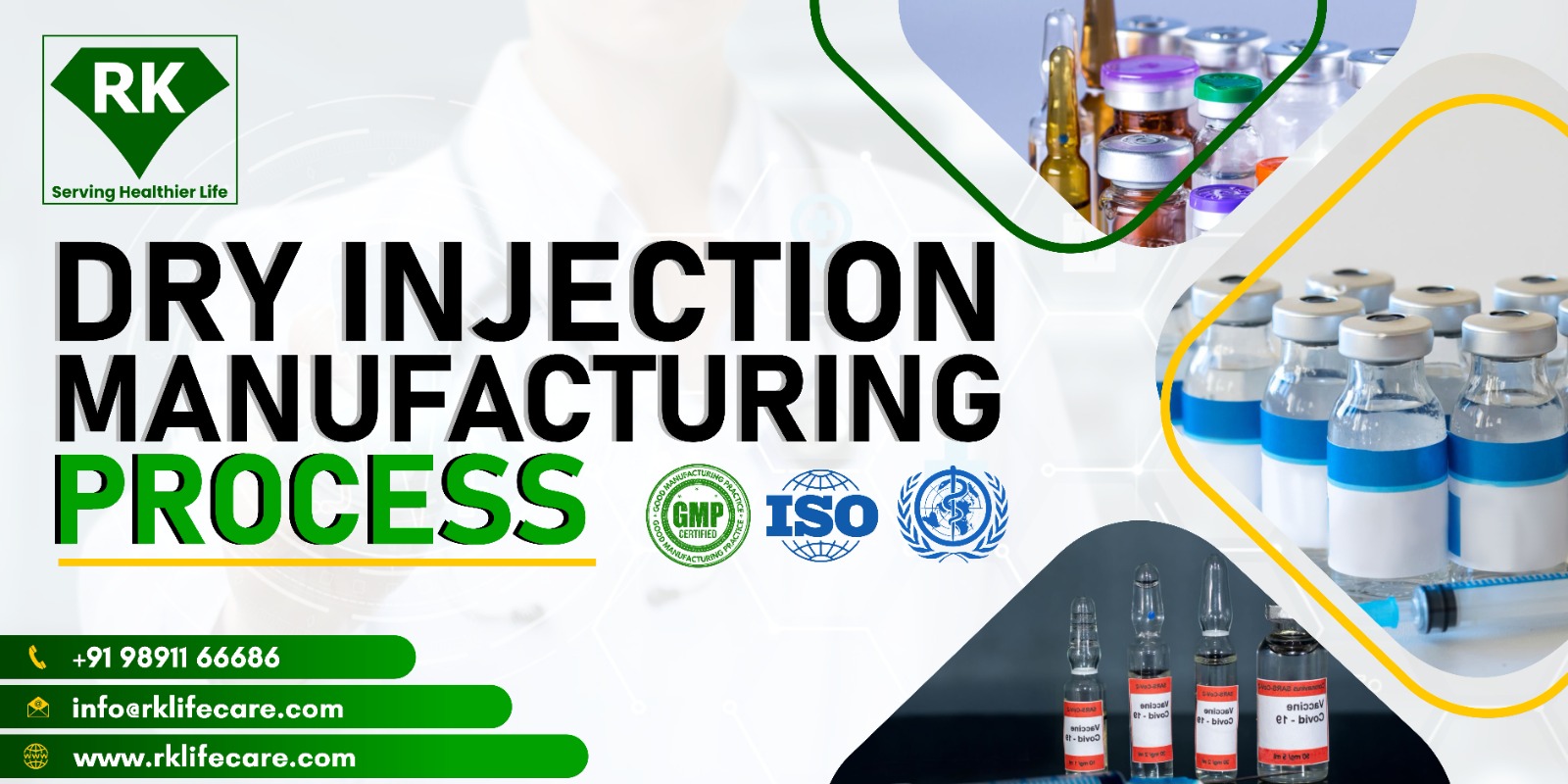
21 Feb 2025
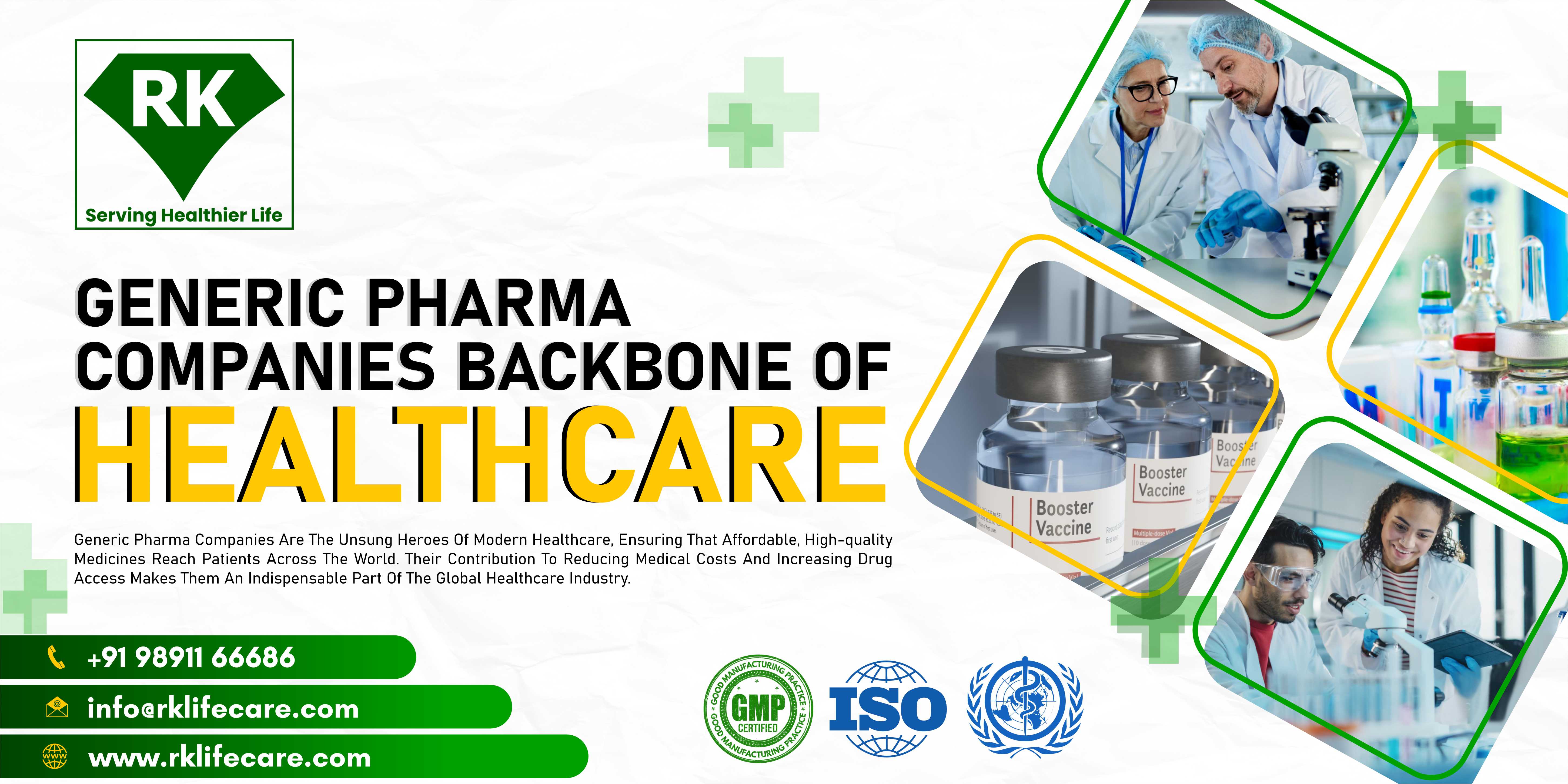
06 Feb 2025
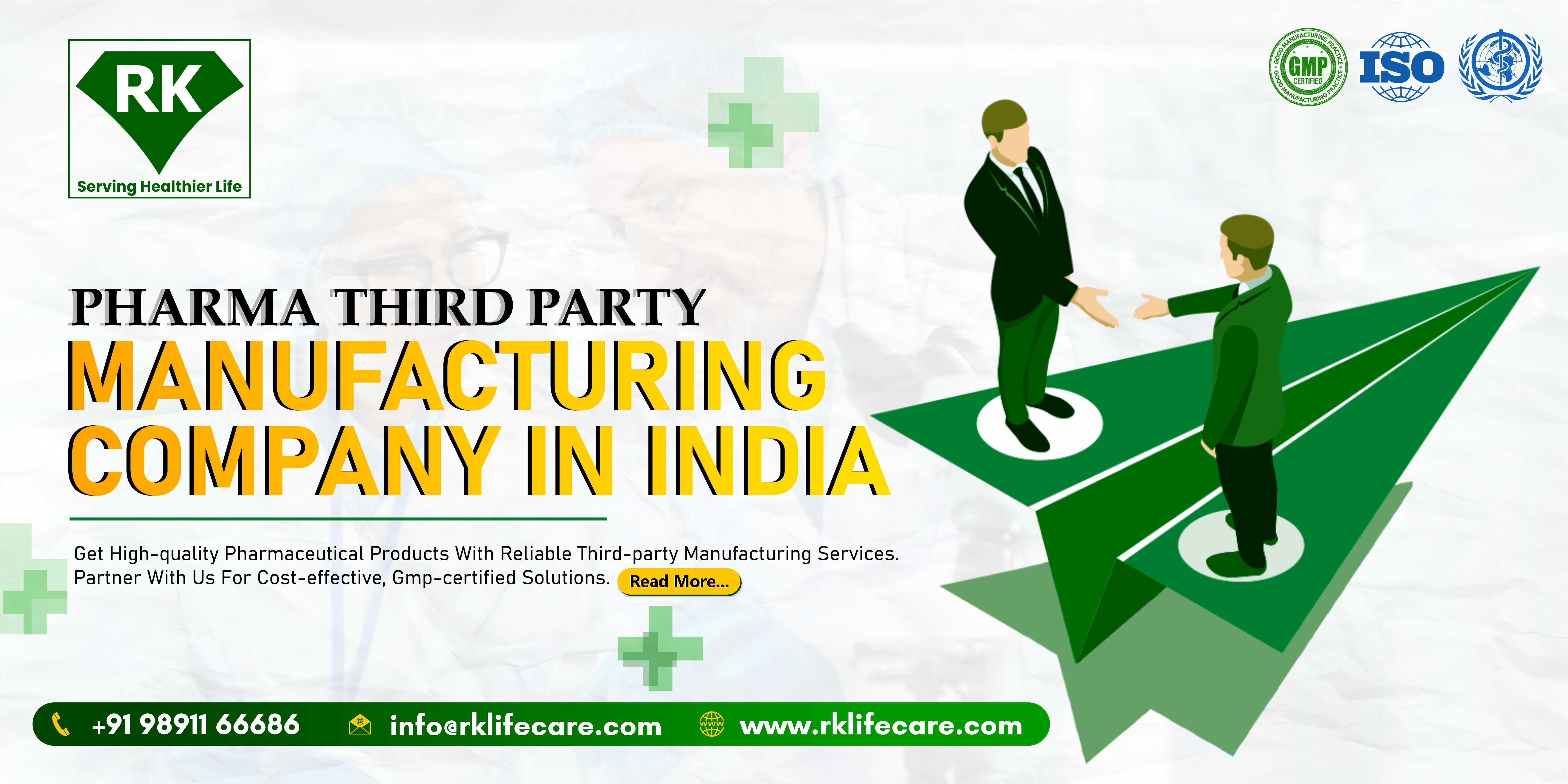
04 Feb 2025
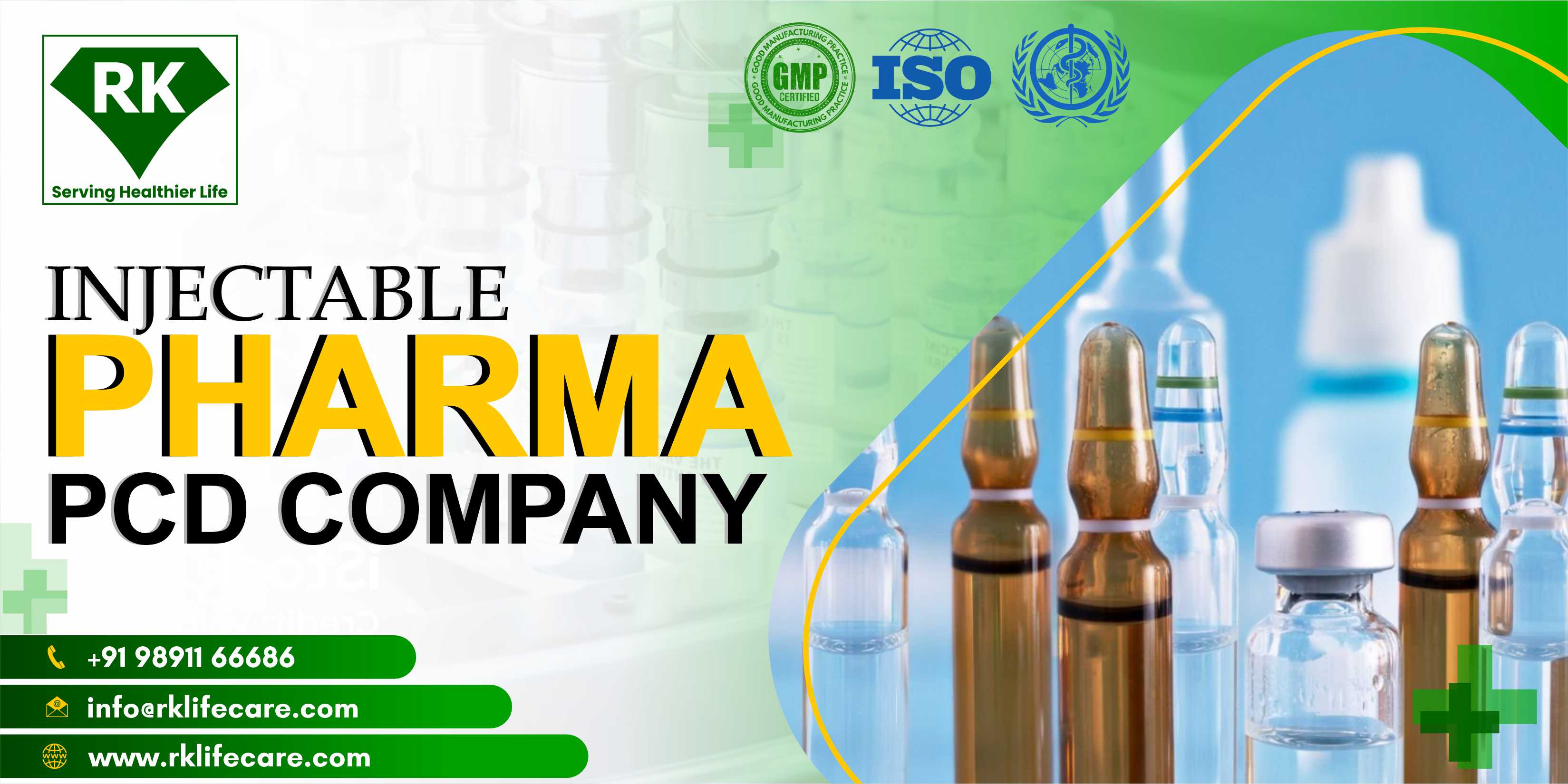
03 Feb 2025
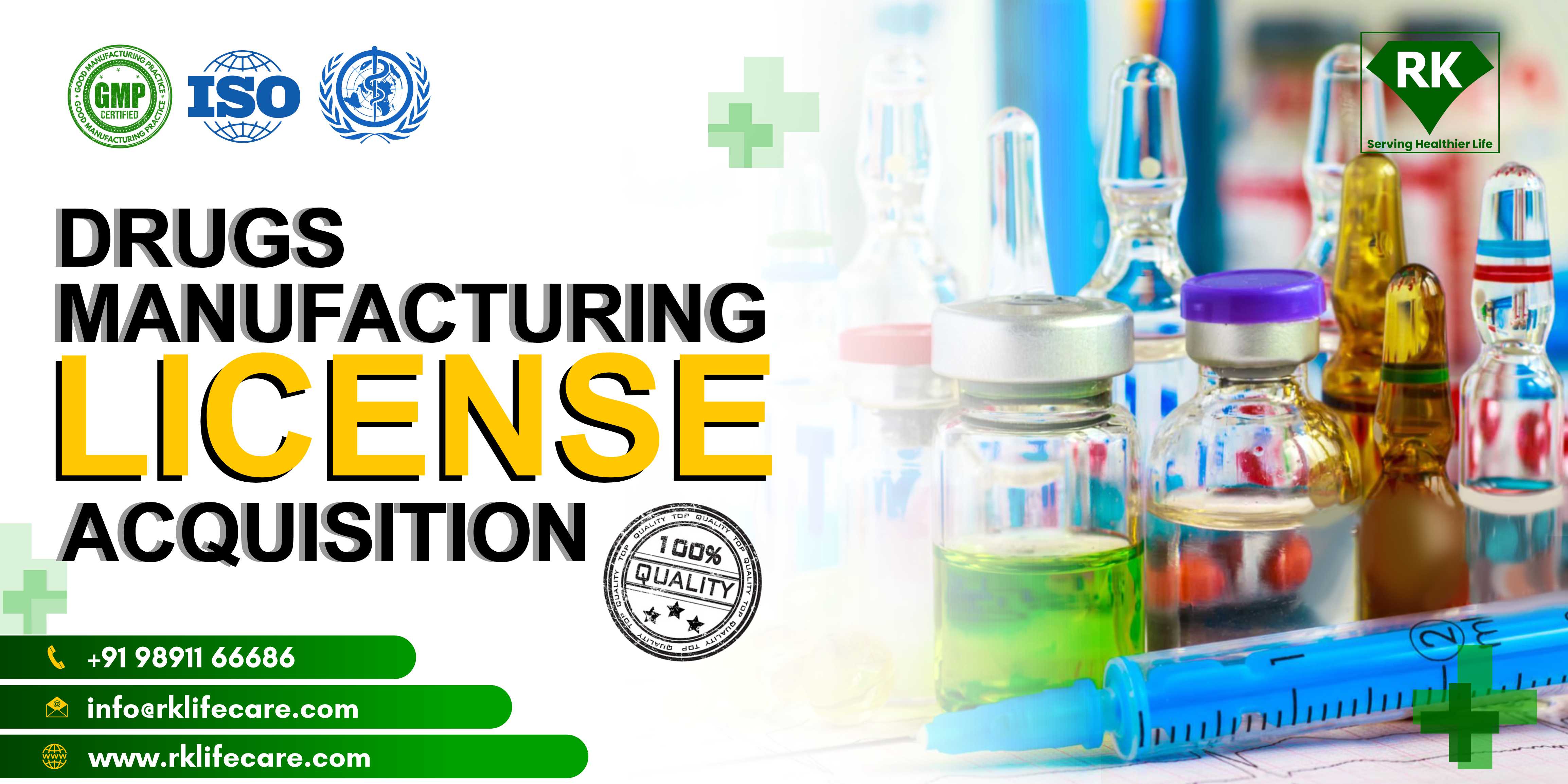
01 Feb 2025
.jpg)
29 Jan 2025
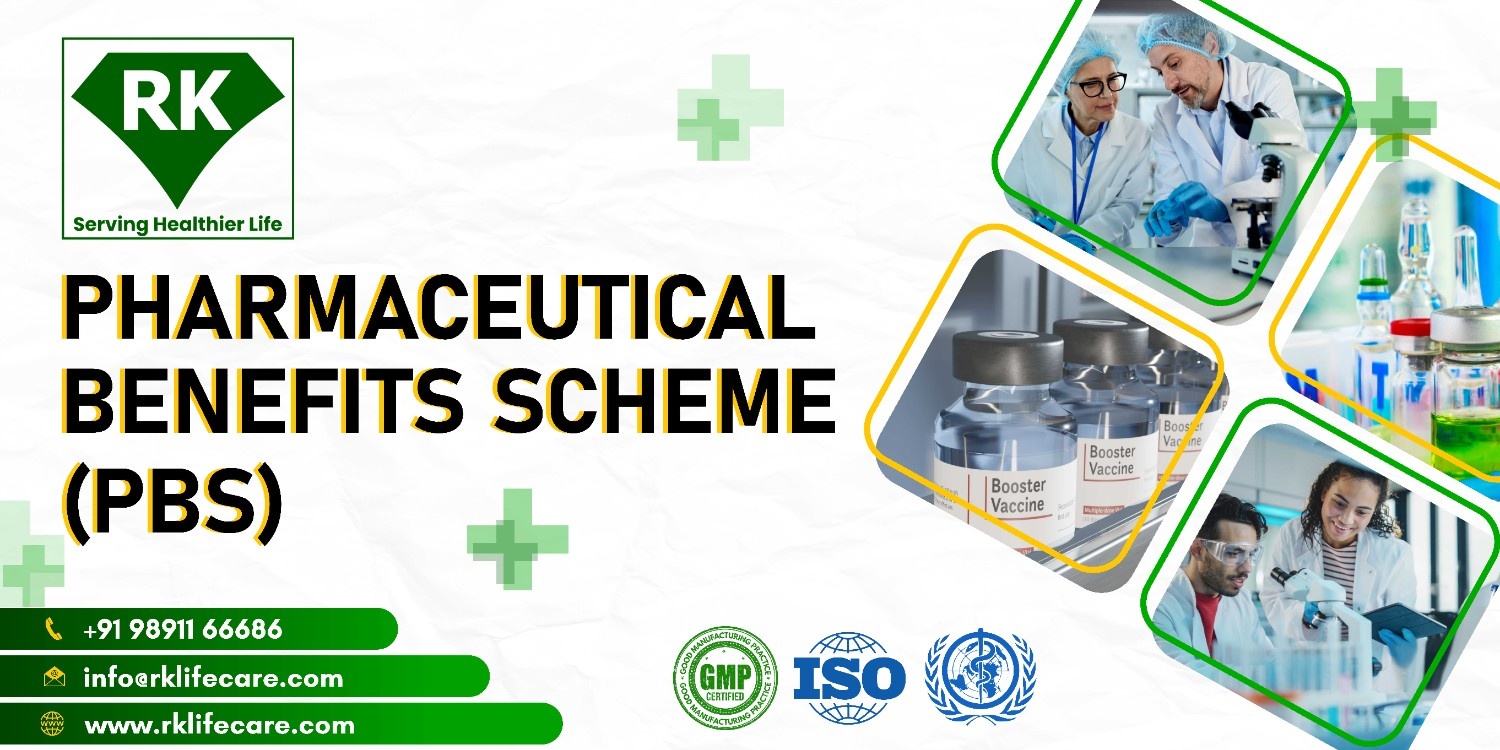
28 Jan 2025
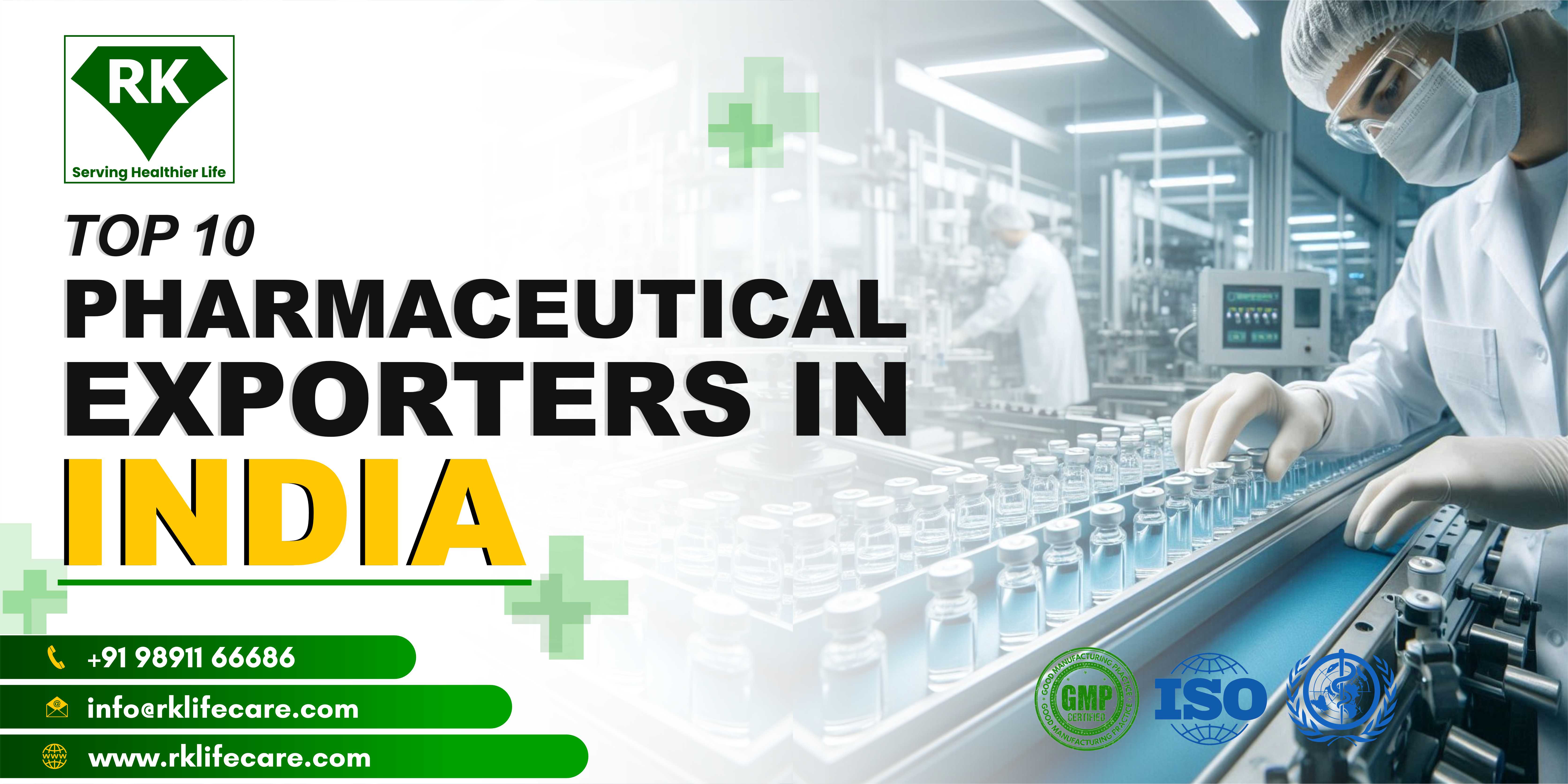
24 Jan 2025
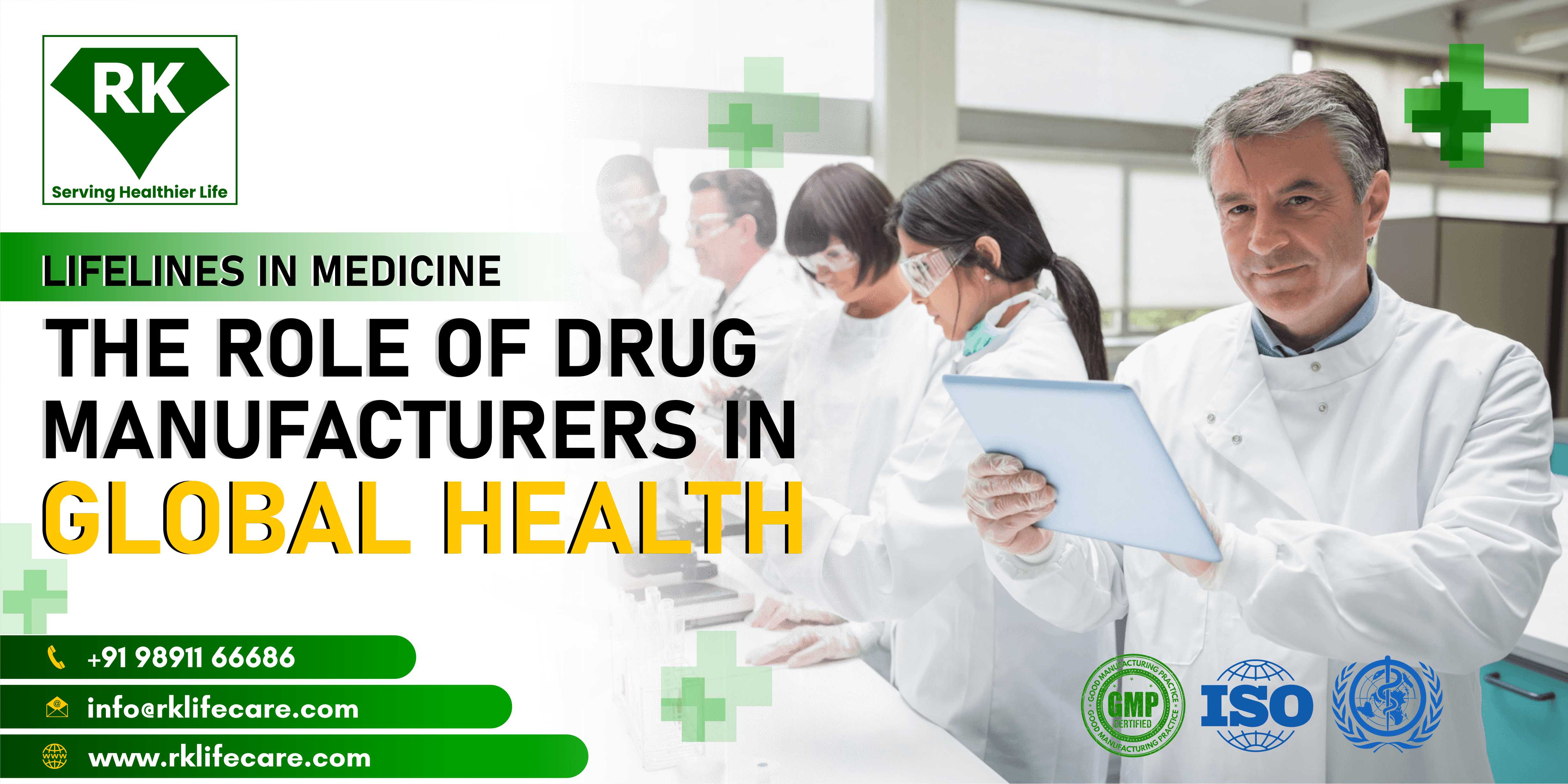
22 Jan 2025
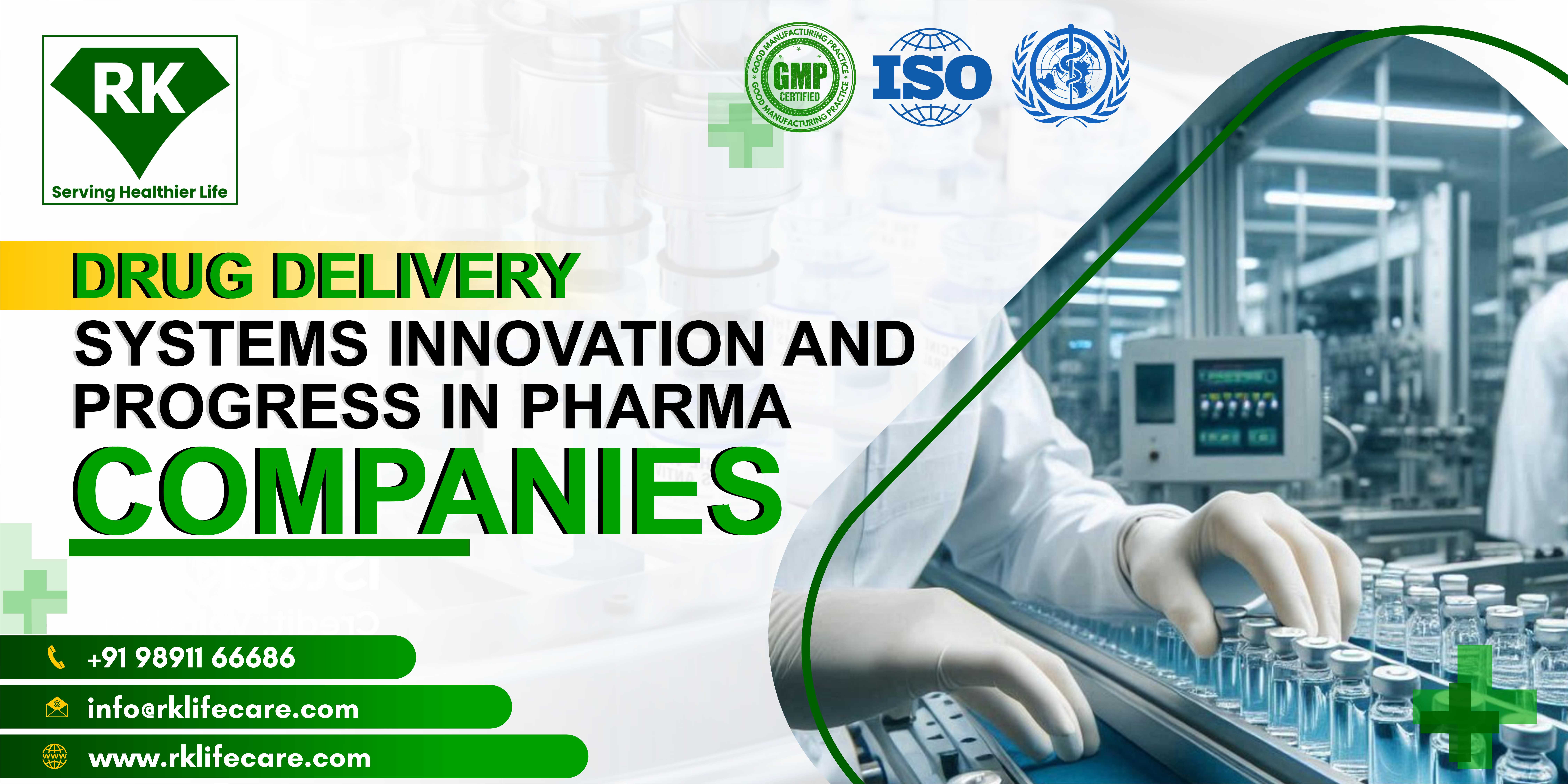
21 Jan 2025
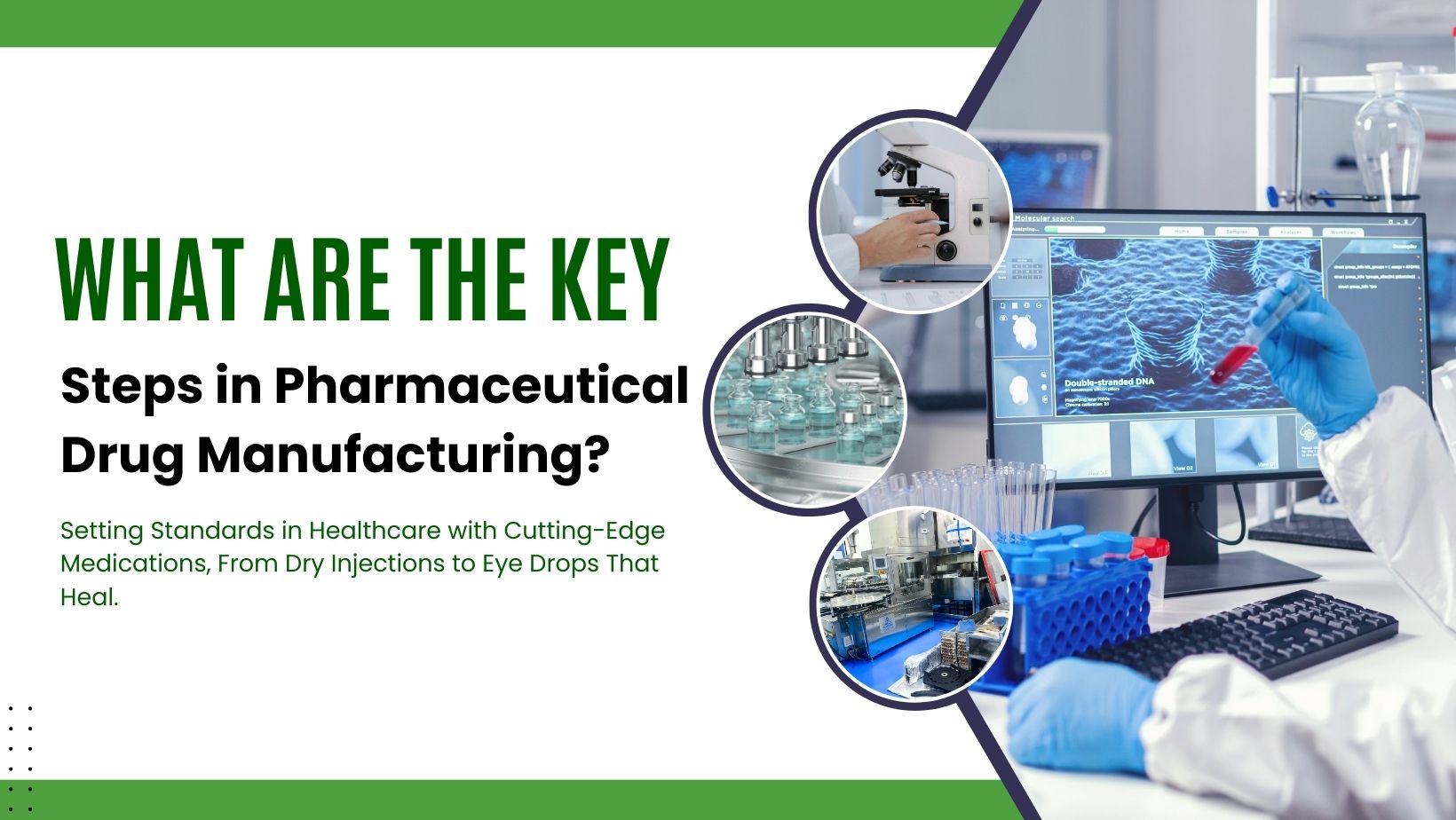
14 Jan 2025
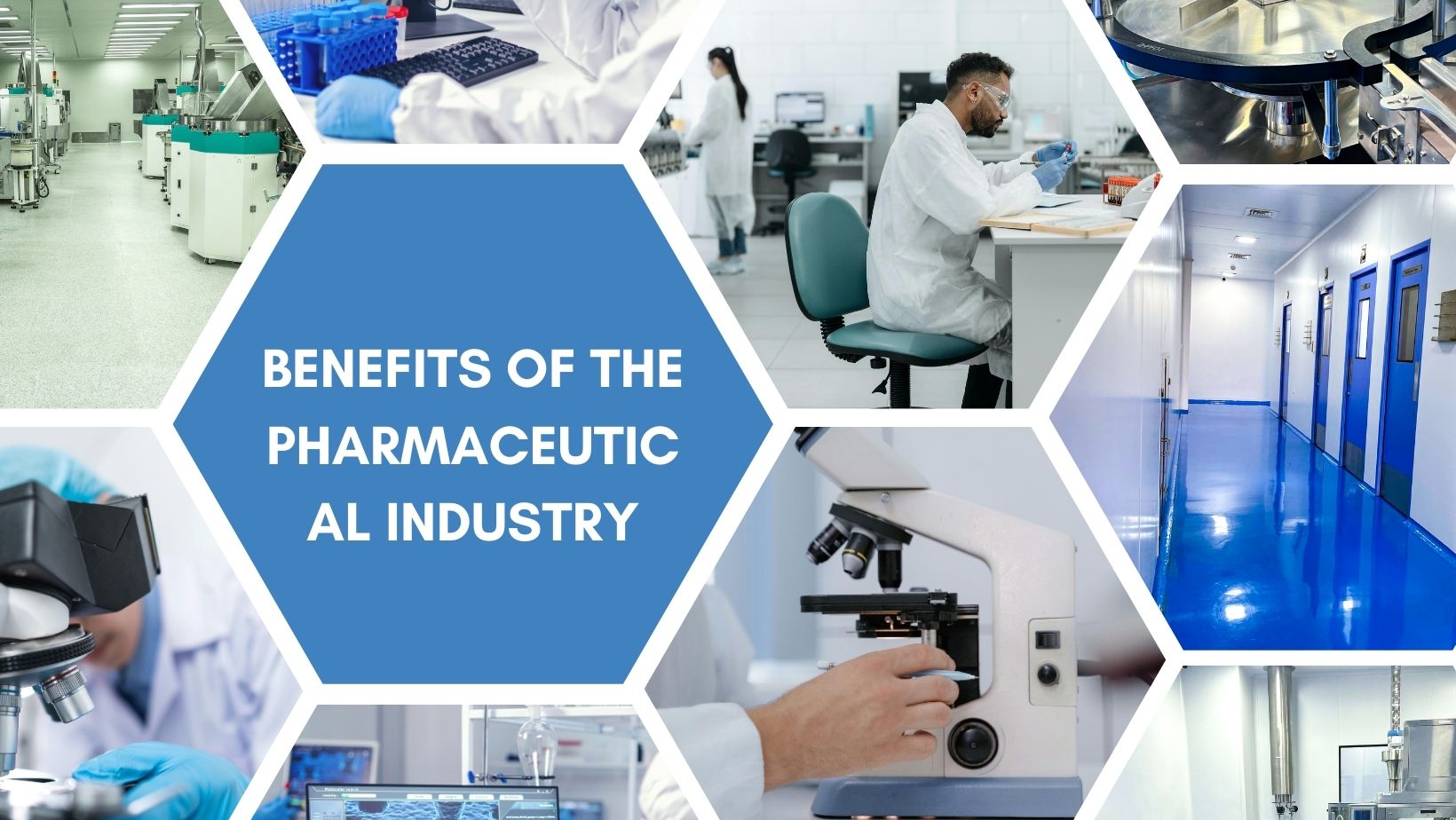
11 Jan 2025
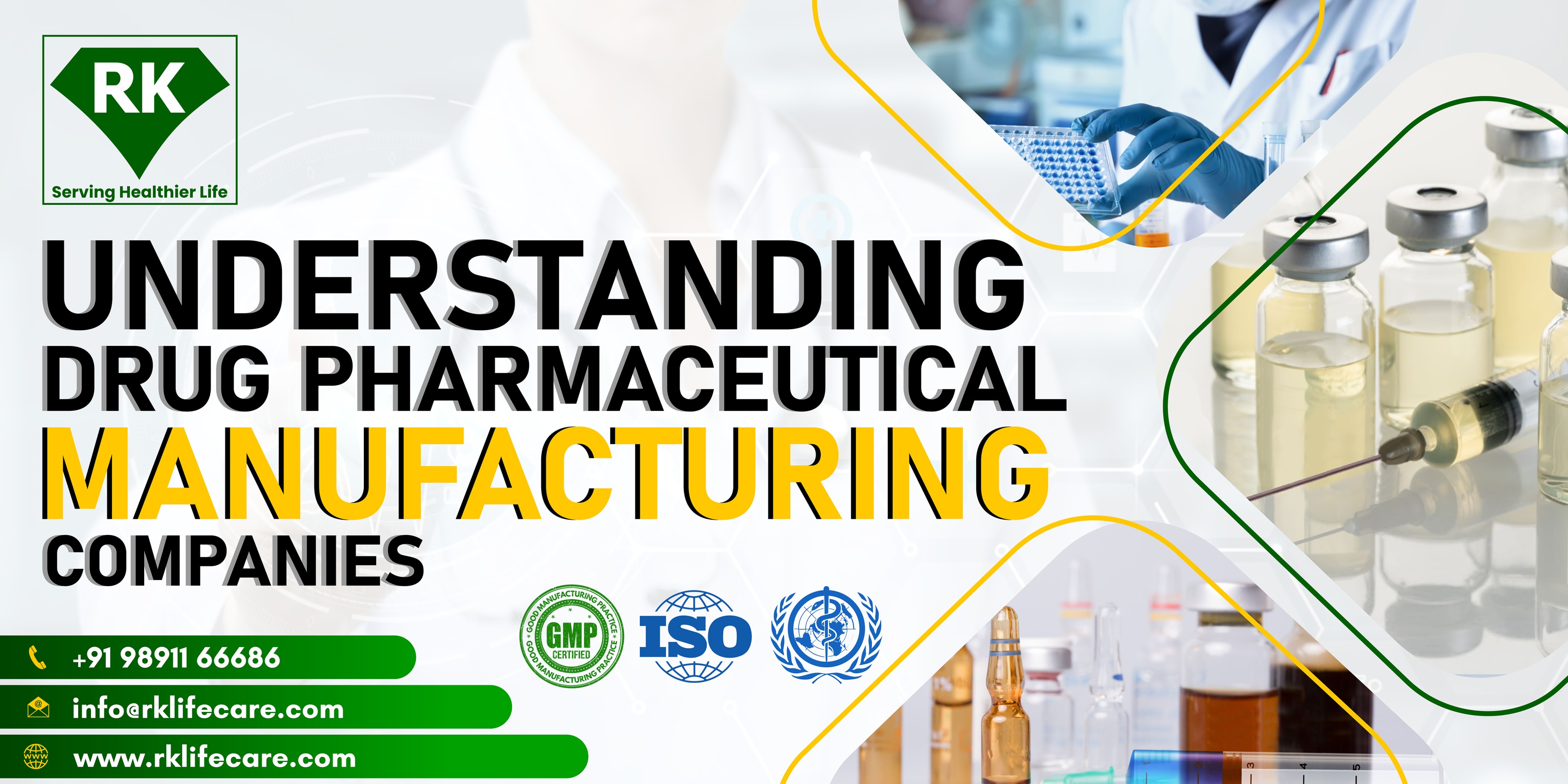
10 Jan 2025
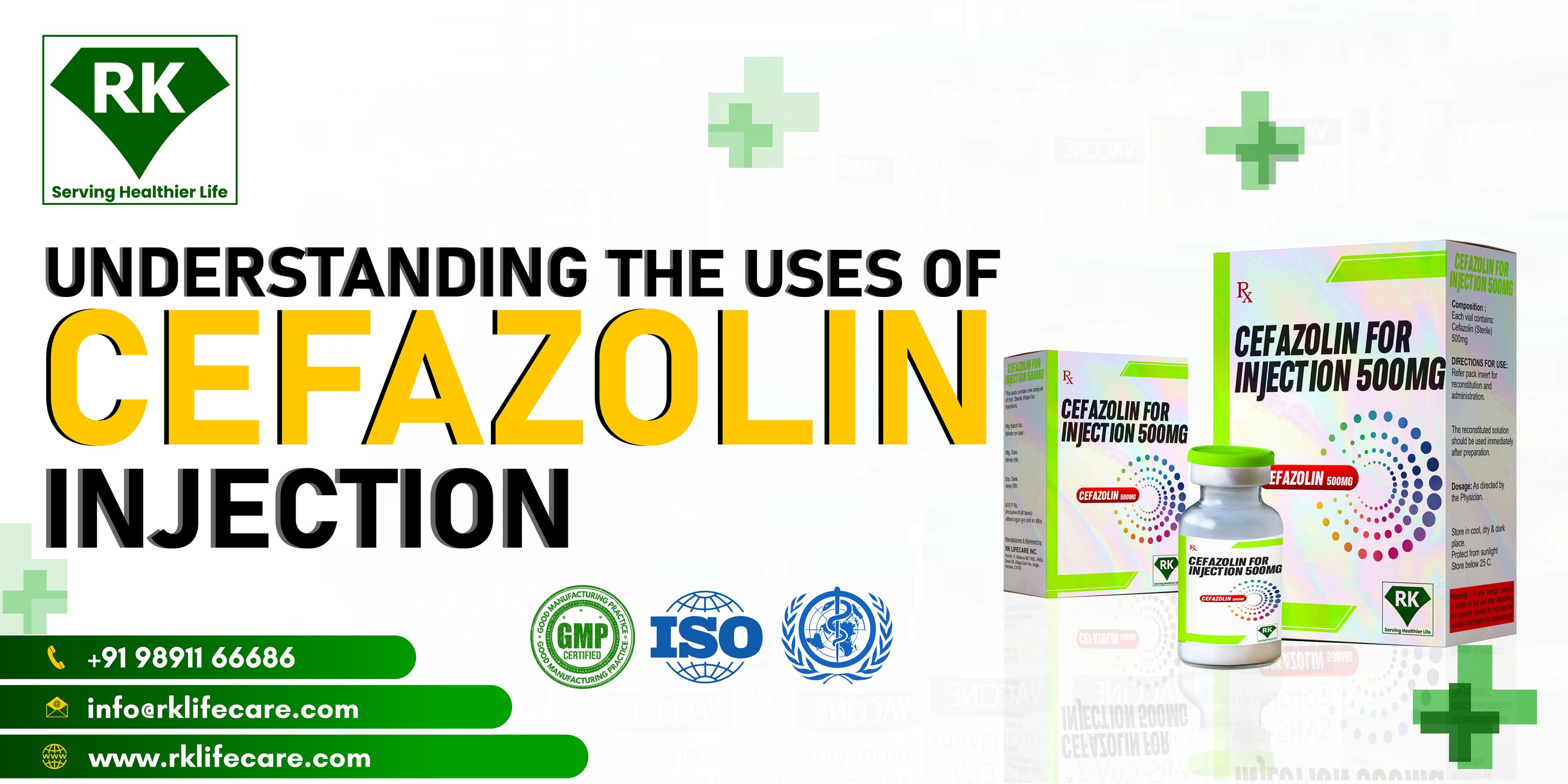
09 Jan 2025
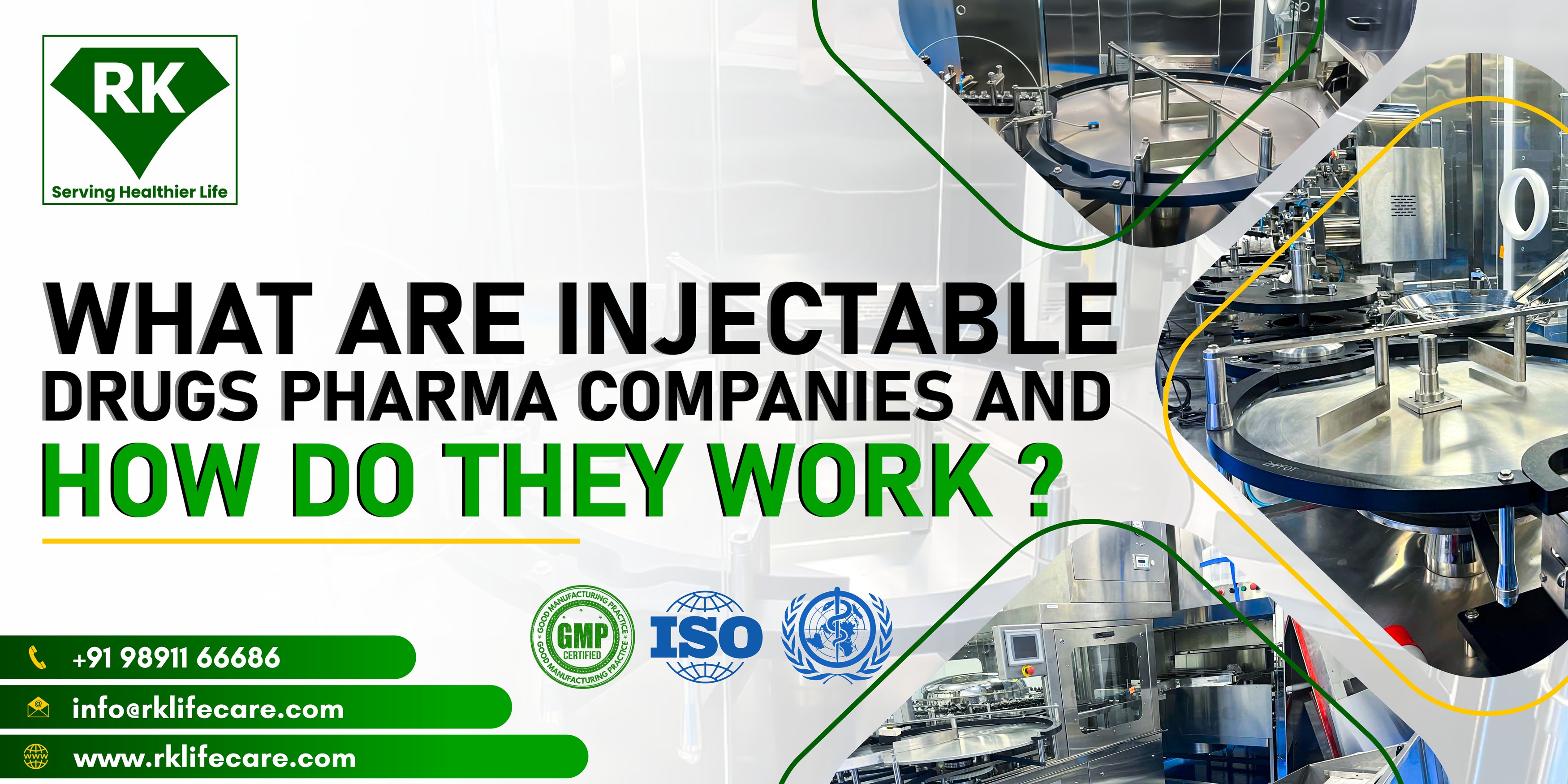
08 Jan 2025