.jpg)
The supply chain of injectable pharmaceuticals is a highly complex and regulated process involving multiple stakeholders. From the procurement of raw materials to the final distribution of products, every step plays a vital role in ensuring the quality, safety, and efficacy of drugs. Pharmaceutical injectables manufacturers must adhere to stringent regulatory guidelines to maintain the highest standards.
In this article, we will discuss the complex supply chain of injectable pharma in detail, covering aspects such as raw material sourcing, manufacturing process, quality control, packaging, storage, and distribution. We will also highlight the role of injectable pharmaceutical companies in India and their contribution to the global healthcare sector.
1. Raw Material Procurement
The supply chain begins with the procurement of active pharmaceutical ingredients (APIs) and excipients needed to manufacture injectables. APIs are the essential components that produce the intended therapeutic effect, while excipients enhance the stability and delivery of the drug.
Key Considerations in Raw Material Sourcing
-
Compliance with Good Manufacturing Practices (GMP)
-
Procurement from certified and reliable suppliers
-
Stringent quality checks to ensure purity and potency
-
Supply chain risk assessment to avoid shortages
Leading pharma injection manufacturers establish strong relationships with reliable API suppliers to ensure consistent availability of high-quality raw materials.
2. Manufacturing Process of Injectable Pharmaceuticals
The production of injectable drugs is a complex process that requires state-of-the-art technology, strict hygiene standards and compliance with regulatory guidelines. The major steps involved in pharma injection manufacturing in India are as follows:
a) Formulation Development
Before mass production, pharmaceutical companies conduct extensive research to develop a stable and effective formulation. Factors such as solubility, stability, and sterility are evaluated in this stage.
b) Sterile Manufacturing Environment
Injections are inserted directly into the bloodstream, making sterility a top priority. Pharma injection manufacturers work in aseptic conditions to prevent contamination. The following protocols are followed:
-
Use of cleanrooms with controlled environments
-
High-Efficiency Particulate Air (HEPA) filtration
-
Proper gowning procedures for personnel
c) Compounding and Mixing
The API and excipients are mixed under sterile conditions to form the final injectable solution or suspension. The mixing process ensures uniformity and consistency in the potency of the drug.
d) Filtration and Sterilization
To eliminate any microbial contamination, the solution is filtered and sterilized. Common sterilization methods include:
-
Filtration through 0.22-micron filters
-
Heat sterilization (autoclaving)
-
Gamma irradiation
e) Filling and Sealing
Once sterilized, the injectable drug is filled into vials, vials, or pre-filled syringes under strict aseptic conditions. The containers are then sealed to maintain sterility.
3. Quality Control and Testing
Ensuring the safety and efficacy of injectable pharmaceuticals is a top priority for injectable pharma companies. The manufacturing process involves rigorous quality control (QC) measures, including:
-
Microbiological Testing – To detect bacterial, fungal, or viral contaminants
-
Sterility Testing – Ensuring the product remains free from microbial contamination
-
Potency and Stability Testing – Confirming the drug maintains its therapeutic effectiveness over time
-
Particulate Matter Analysis – Detecting unwanted particles that could cause adverse reactions
Regulatory bodies in India such as the FDA, WHO, and CDSCO have set strict guidelines that top injectable drug companies in India must follow to ensure patient safety.
4. Packaging and Labeling
Proper packaging plays a vital role in maintaining the stability and sterility of injectable drugs. Pharma injection manufacturers use special materials to prevent degradation caused by light, temperature, and humidity.
Types of Packaging for Injectables:
-
Glass Vials – Ideal for liquid injectables
-
Ampoules – Single-dose packaging to prevent contamination
-
Pre-Filled Syringes – Convenient for self-administration
The labeling of injectable drugs must include essential information such as:
-
Drug name and composition
-
Dosage instructions
-
Manufacturing and expiry date
-
Storage conditions
-
Manufacturer details
5. Storage and Cold Chain Management
Many injectables, especially biologic products and vaccines, require specific storage conditions to maintain their efficacy. Injectable pharmaceutical companies in India implement robust cold chain logistics to properly store and transport temperature-sensitive products.
Key Elements of Cold Chain Management:
-
Temperature-Controlled Storage – Refrigerators and freezers with real-time monitoring
-
Cold Chain Transport – Insulated containers, temperature-controlled trucks, and monitoring devices
-
Regulatory Compliance – Adherence to WHO and GMP guidelines for storage and distribution
6. Distribution and Logistics
The final stage of the supply chain involves distributing injectable pharmaceuticals to hospitals, pharmacies, and healthcare providers. Pharma injectable manufacturers collaborate with distributors, wholesalers, and logistics partners to ensure timely and efficient delivery.
Challenges in Injectable Drug Distribution:
-
Maintaining cold chain integrity
-
Regulatory documentation and customs clearance for exports
-
Counterfeit prevention and serialization
7. Regulatory Compliance and Documentation
Manufacturers of injectable medicines must adhere to international and national regulatory standards to ensure product quality and patient safety. In India, the Central Drugs Standard Control Organization (CDSCO) oversees the approval and regulation of injectable medicines.
Key Regulatory Requirements:
-
Drug Master File (DMF) submission
-
Good Manufacturing Practices (GMP) certification
-
Stability and clinical trials documentation
-
Pharmacovigilance reporting for adverse reactions
8. Role of Injectable Pharmaceutical Companies in India
India is a global hub for pharma injection manufacturing, with many top injectable pharmaceutical companies supplying high-quality injectable drugs to domestic and international markets.
Why India is a Leading Supplier of Injectable Pharmaceuticals:
-
Cost-Effective Manufacturing – Lower production costs compared to Western countries
-
High-Quality Standards – Compliance with US FDA, WHO-GMP, and EU GMP guidelines
-
Robust R&D Capabilities – Continuous innovation in formulation development
-
Expanding Global Reach – Exports to over 150 countries
Some of the top injectable pharmaceutical companies in India are known for their expertise in manufacturing sterile injectable products that meet the needs of the human and veterinary healthcare sectors.
Conclusion
The supply chain of injectable pharmaceuticals is a highly complex and regulated process that requires strict quality control at every stage. From raw material procurement to final distribution, pharma injectable manufacturers must ensure product safety, efficacy, and regulatory compliance. India has emerged as a leading player in pharma injectable manufacturing, providing high-quality, cost-effective solutions to the global healthcare industry. With advancements in technology and a focus on innovation, injectable pharmaceutical companies in India continue to shape the future of healthcare by providing safe and effective injectable medicines to patients around the world.
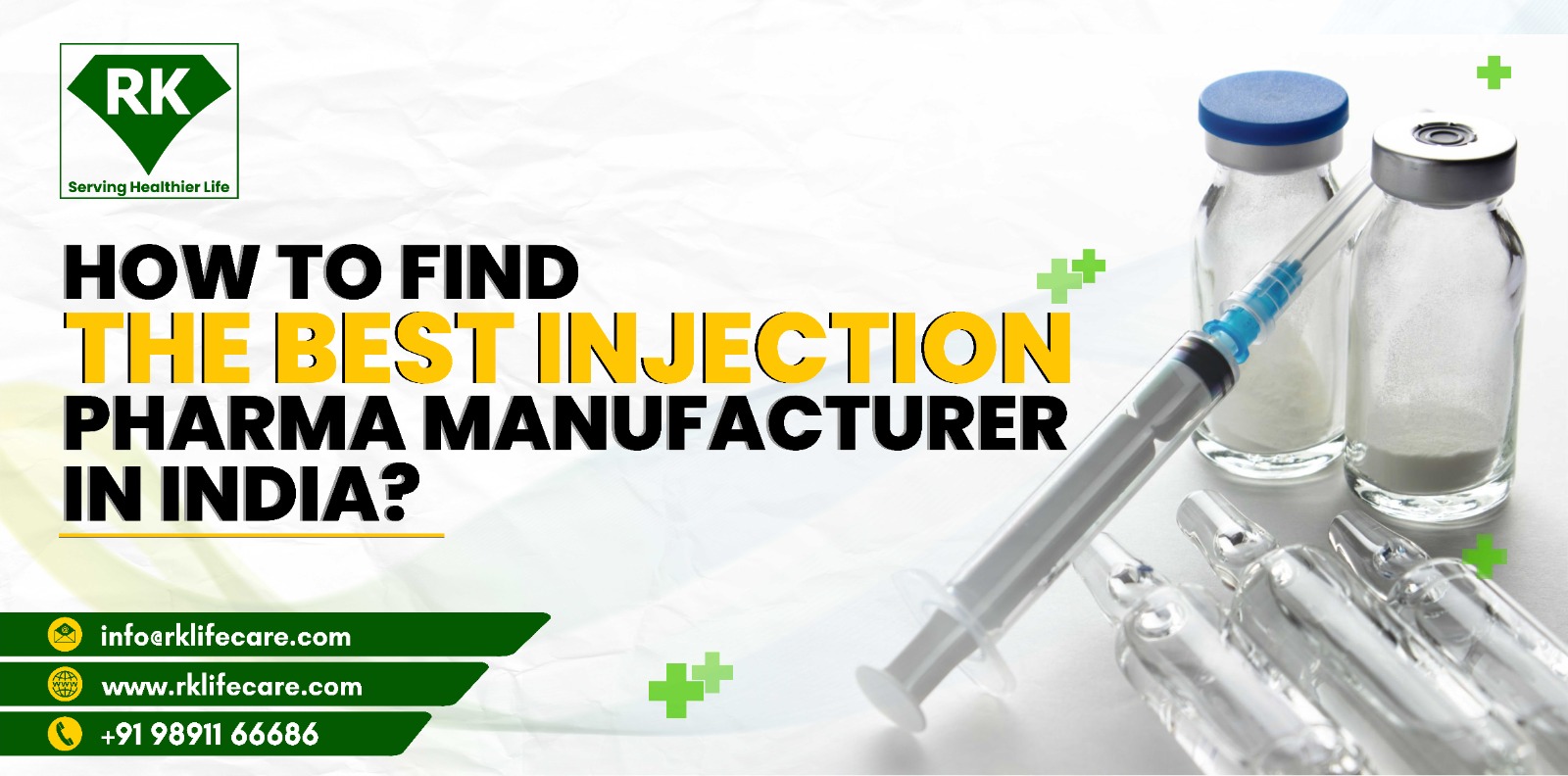
22 Apr 2025
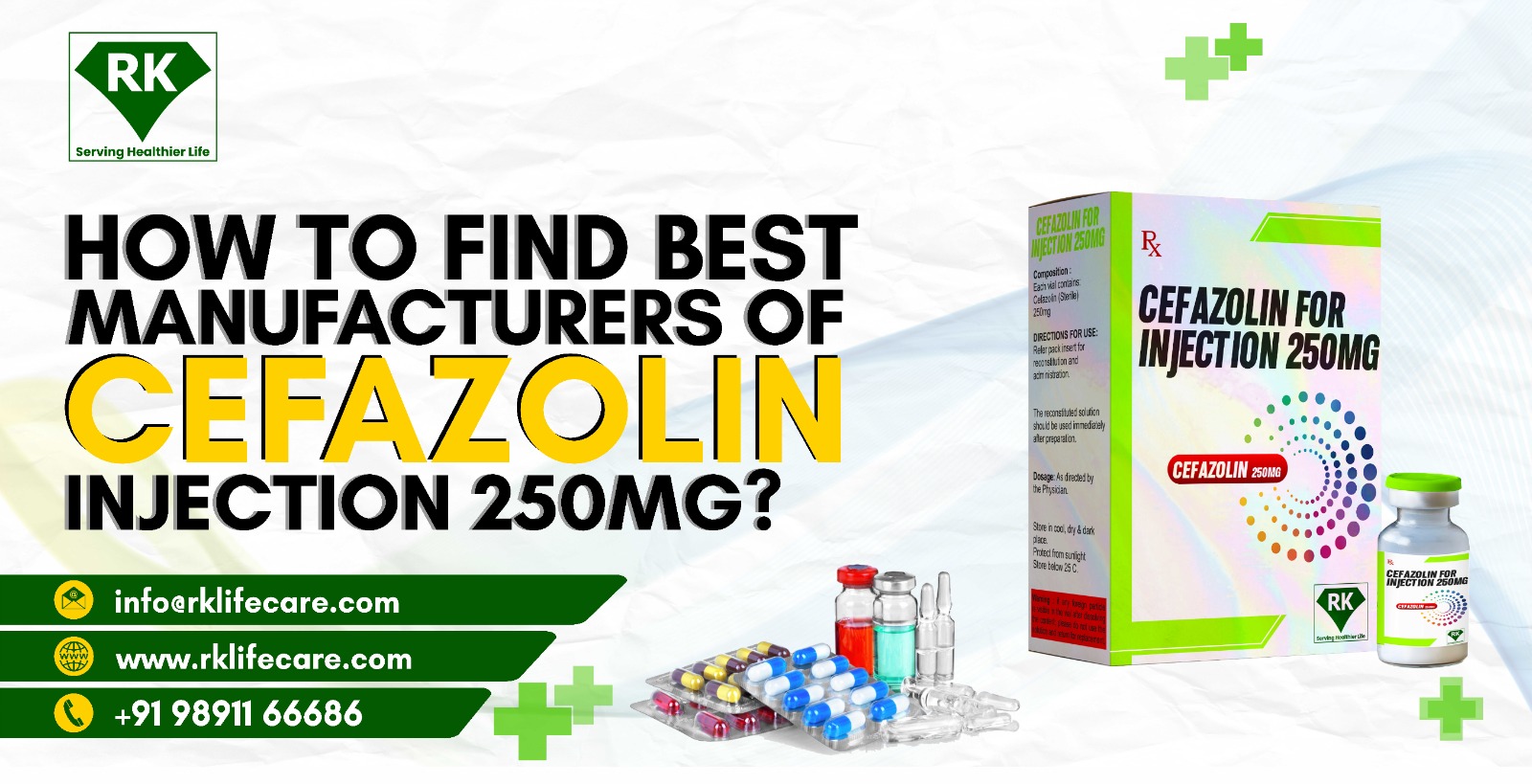
18 Apr 2025
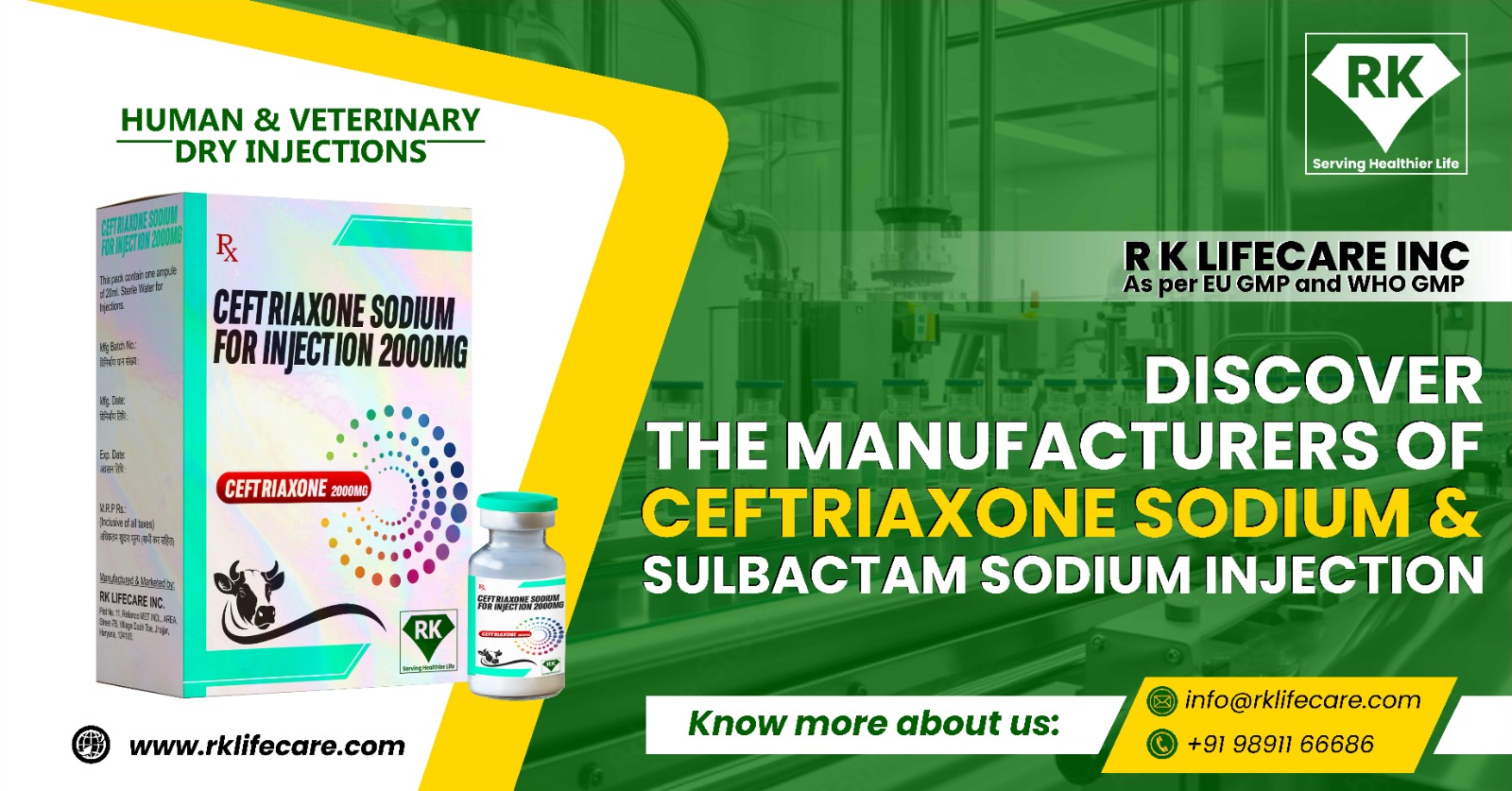
16 Apr 2025
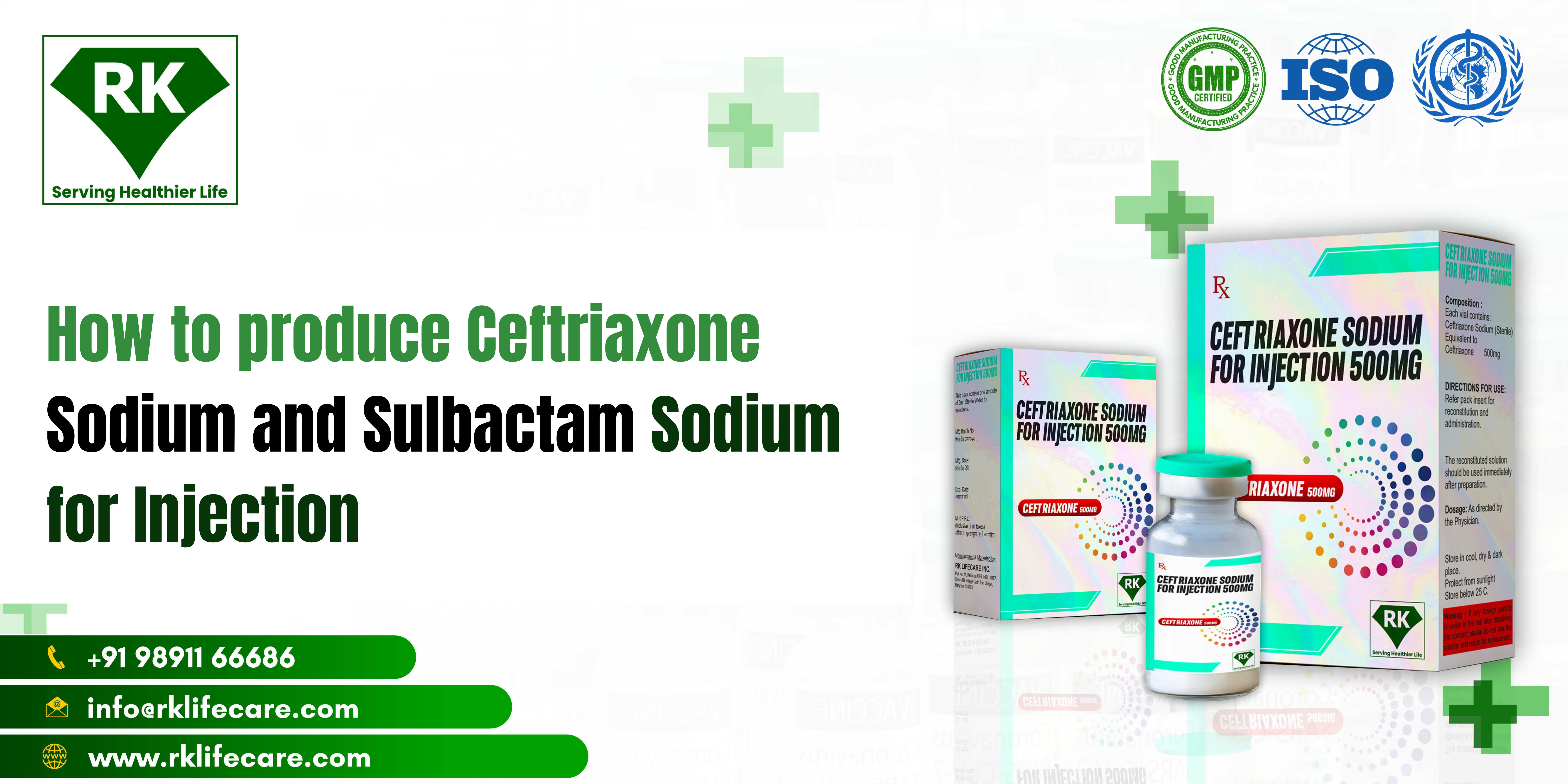
12 Apr 2025
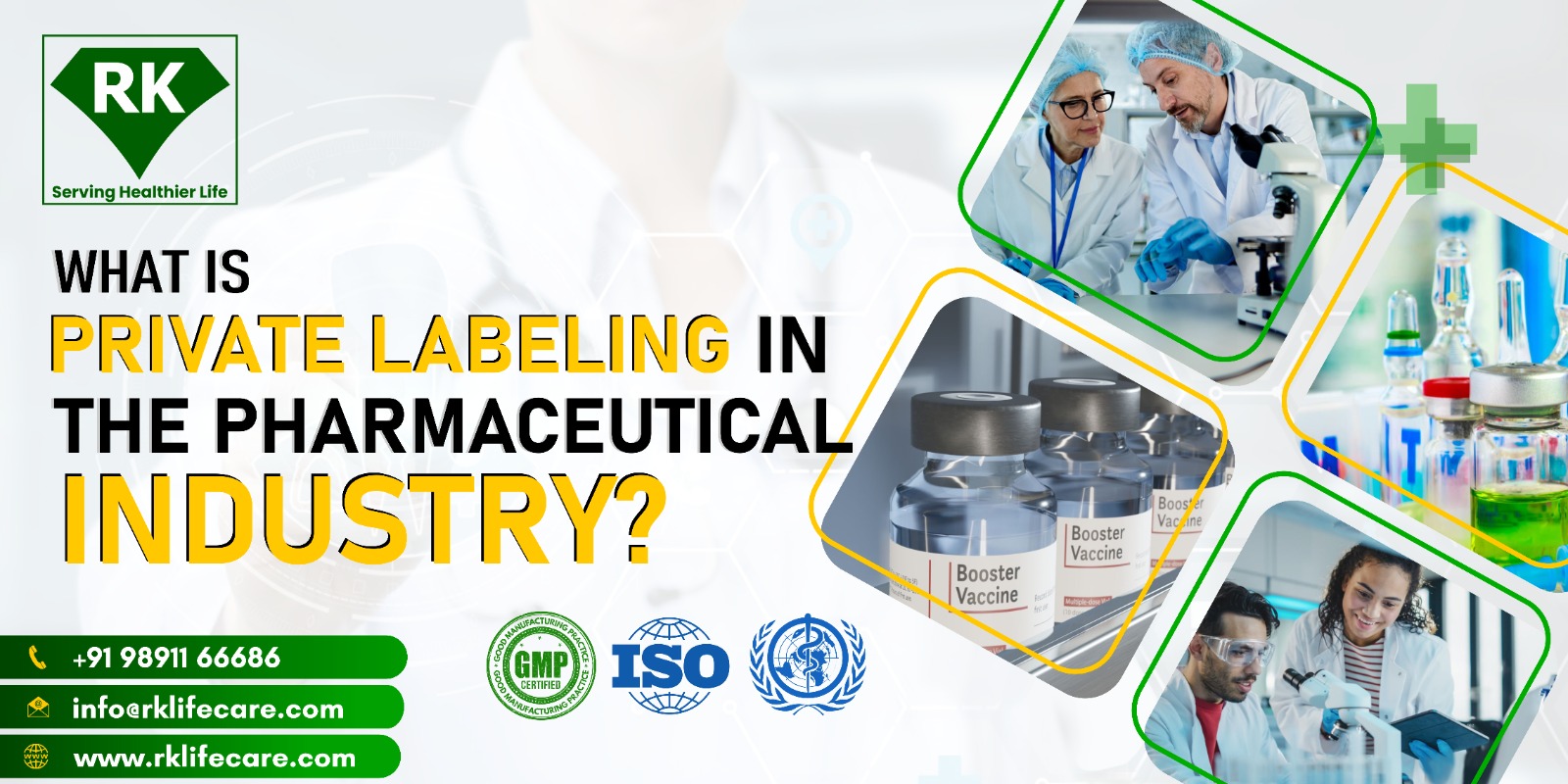
02 Apr 2025
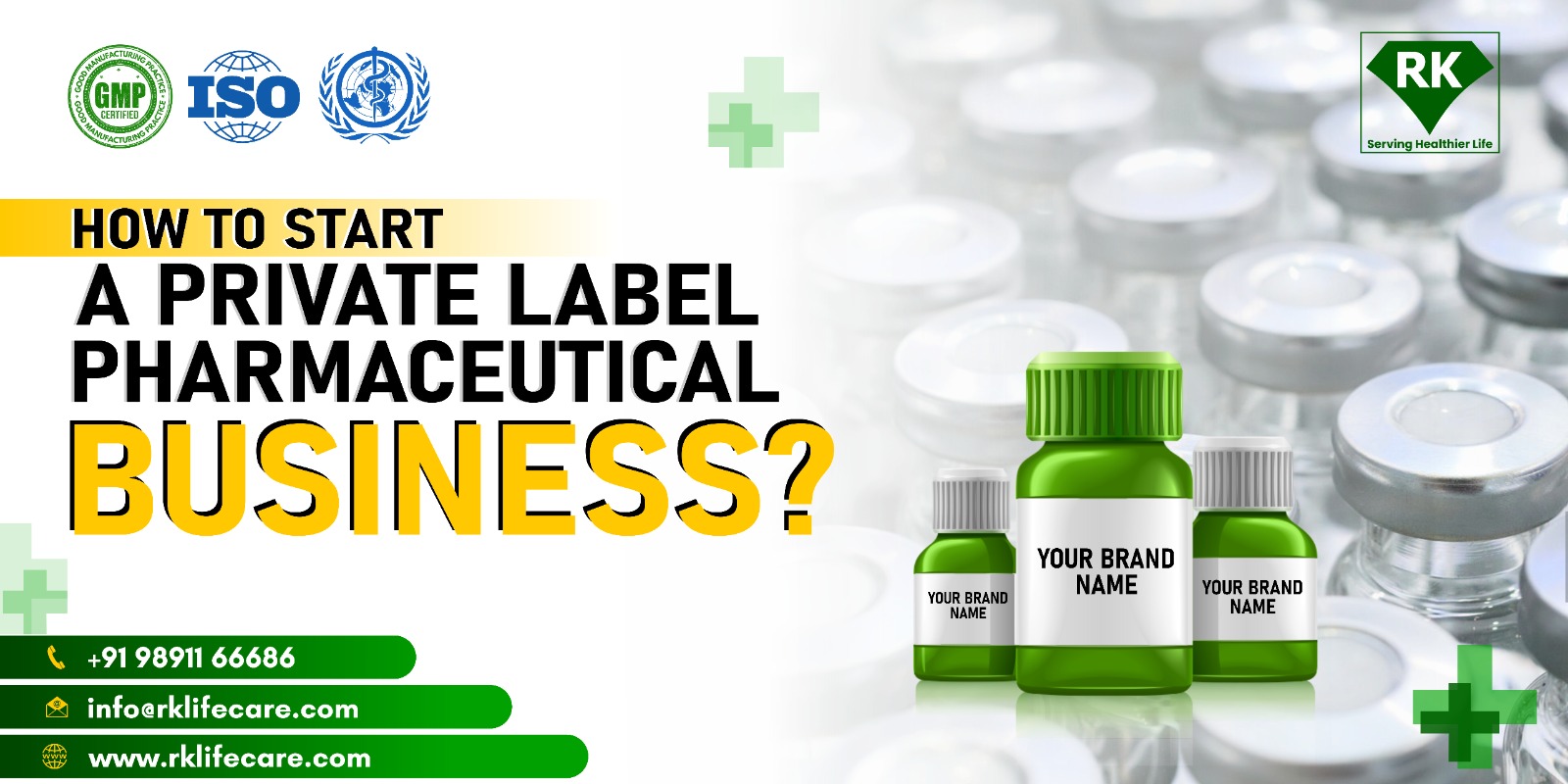
28 Mar 2025
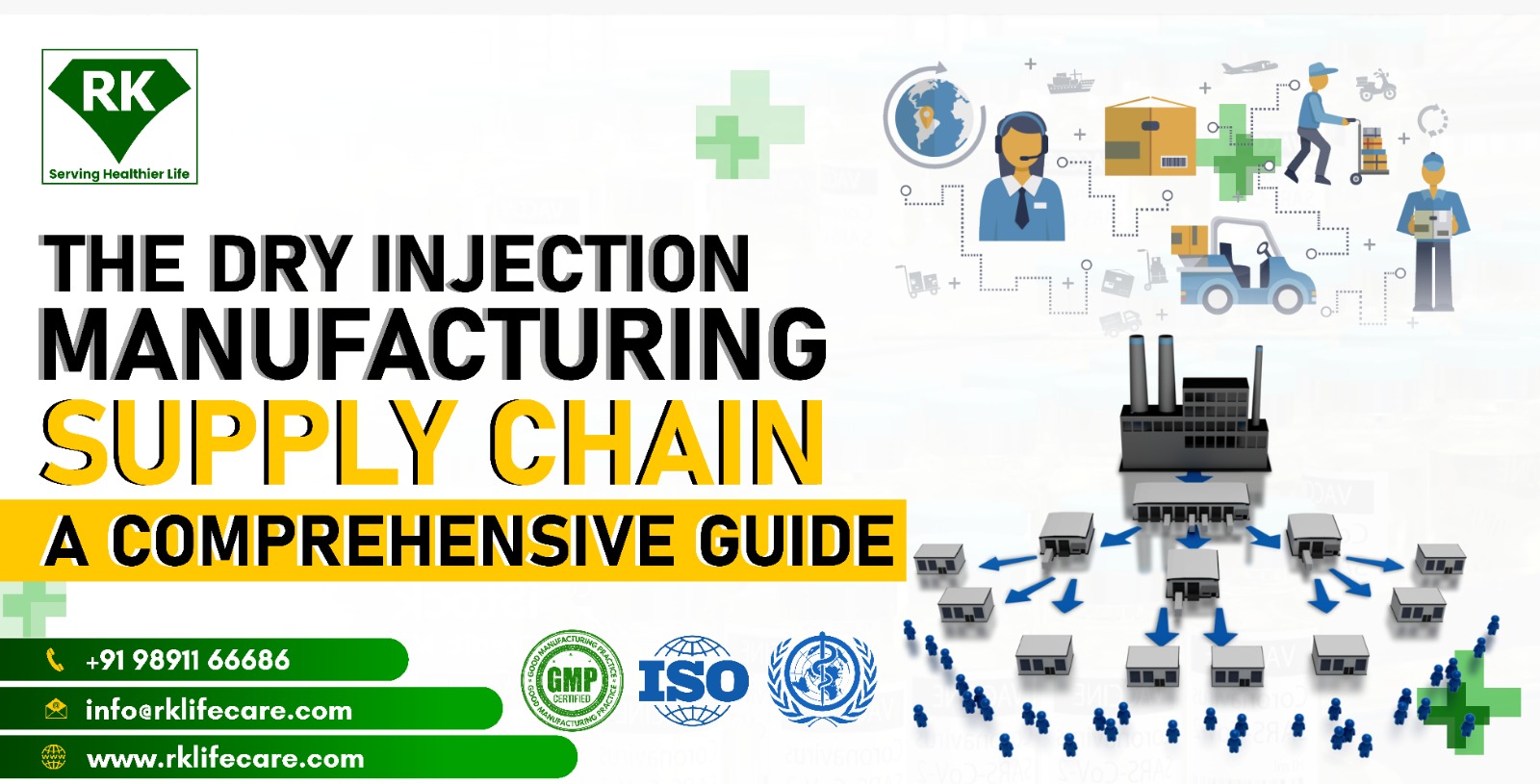
26 Mar 2025
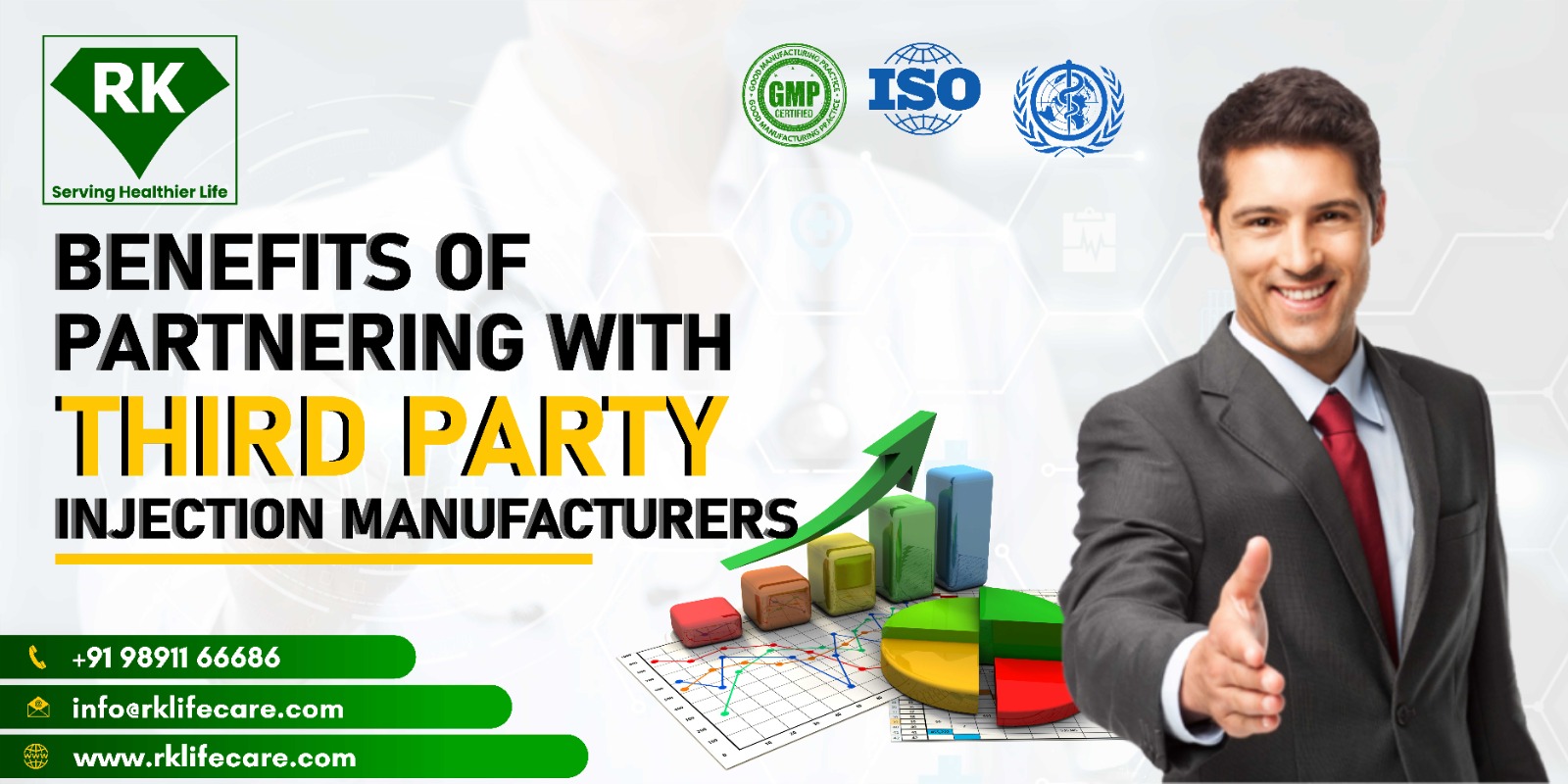
24 Mar 2025
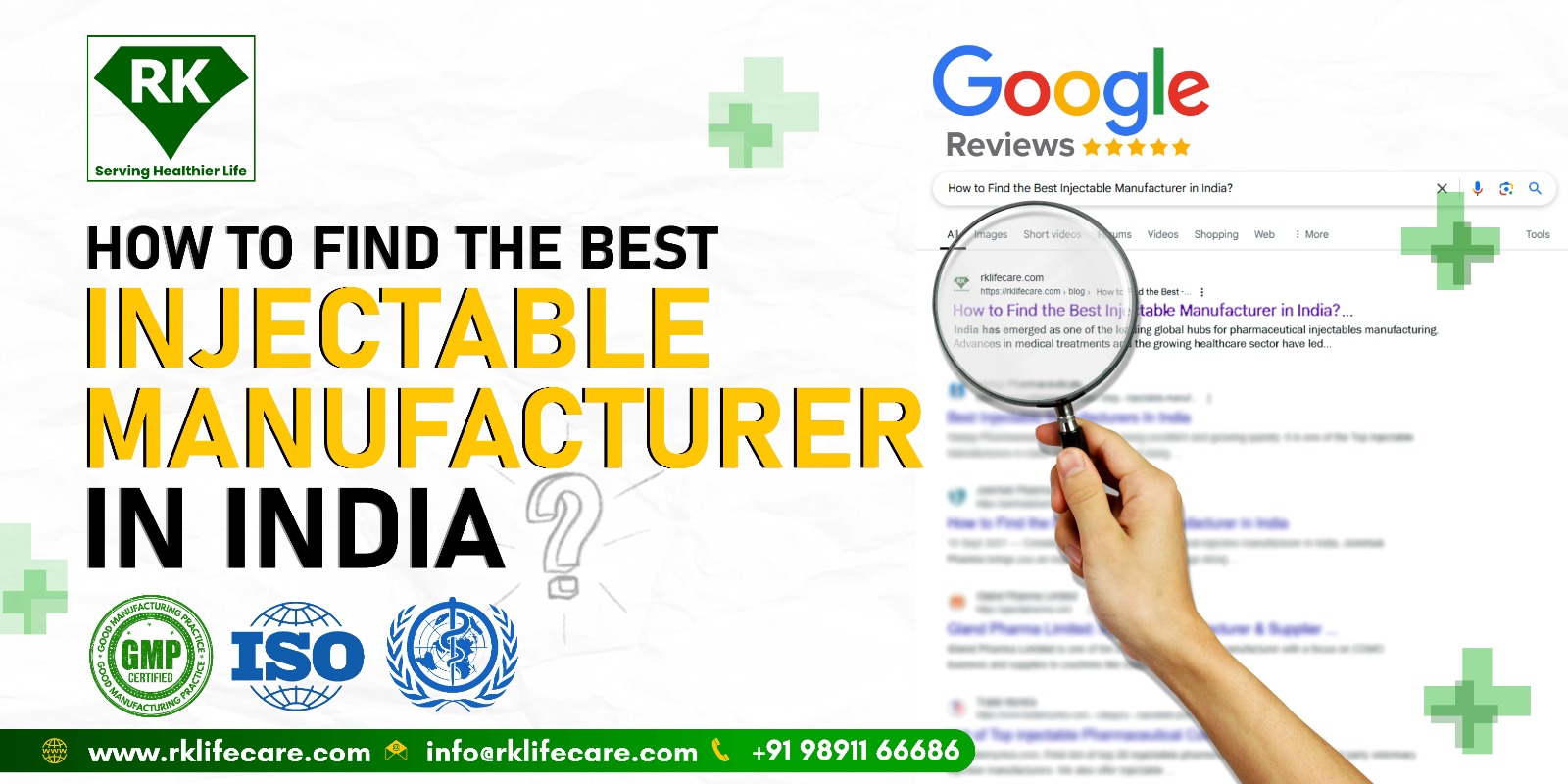
18 Mar 2025
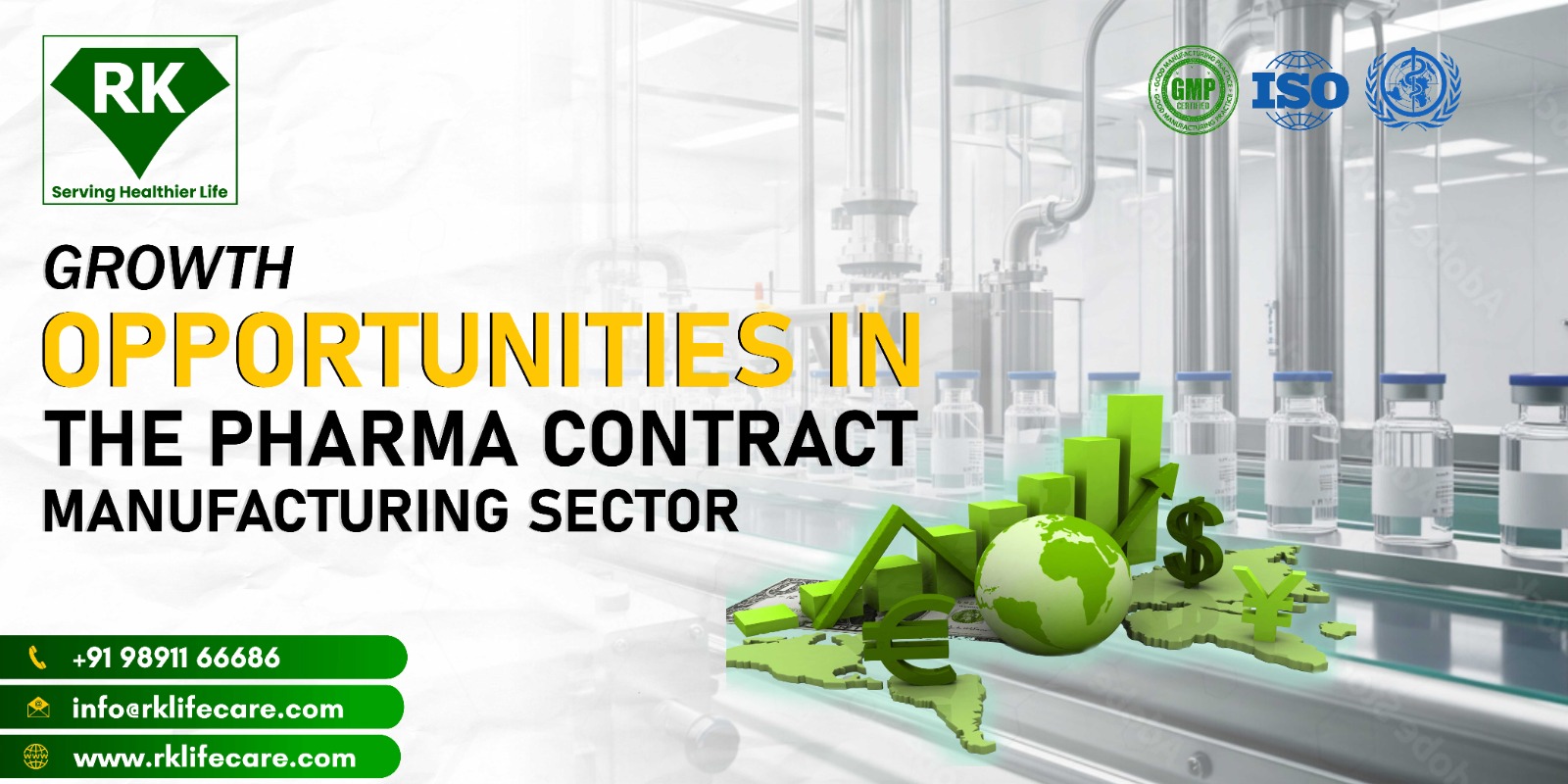
12 Mar 2025
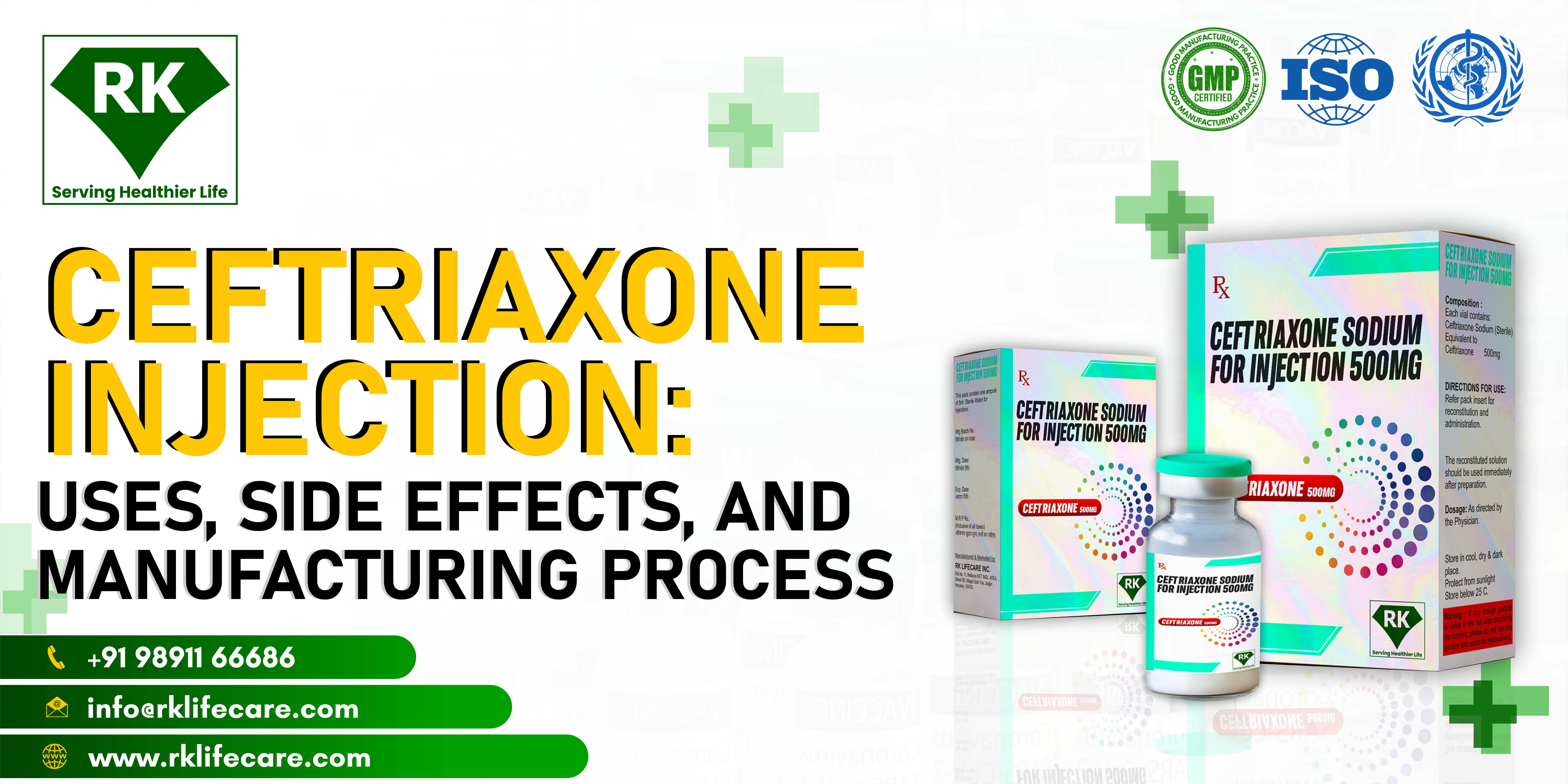
08 Mar 2025
.jpg)
28 Feb 2025
.jpg)
27 Feb 2025
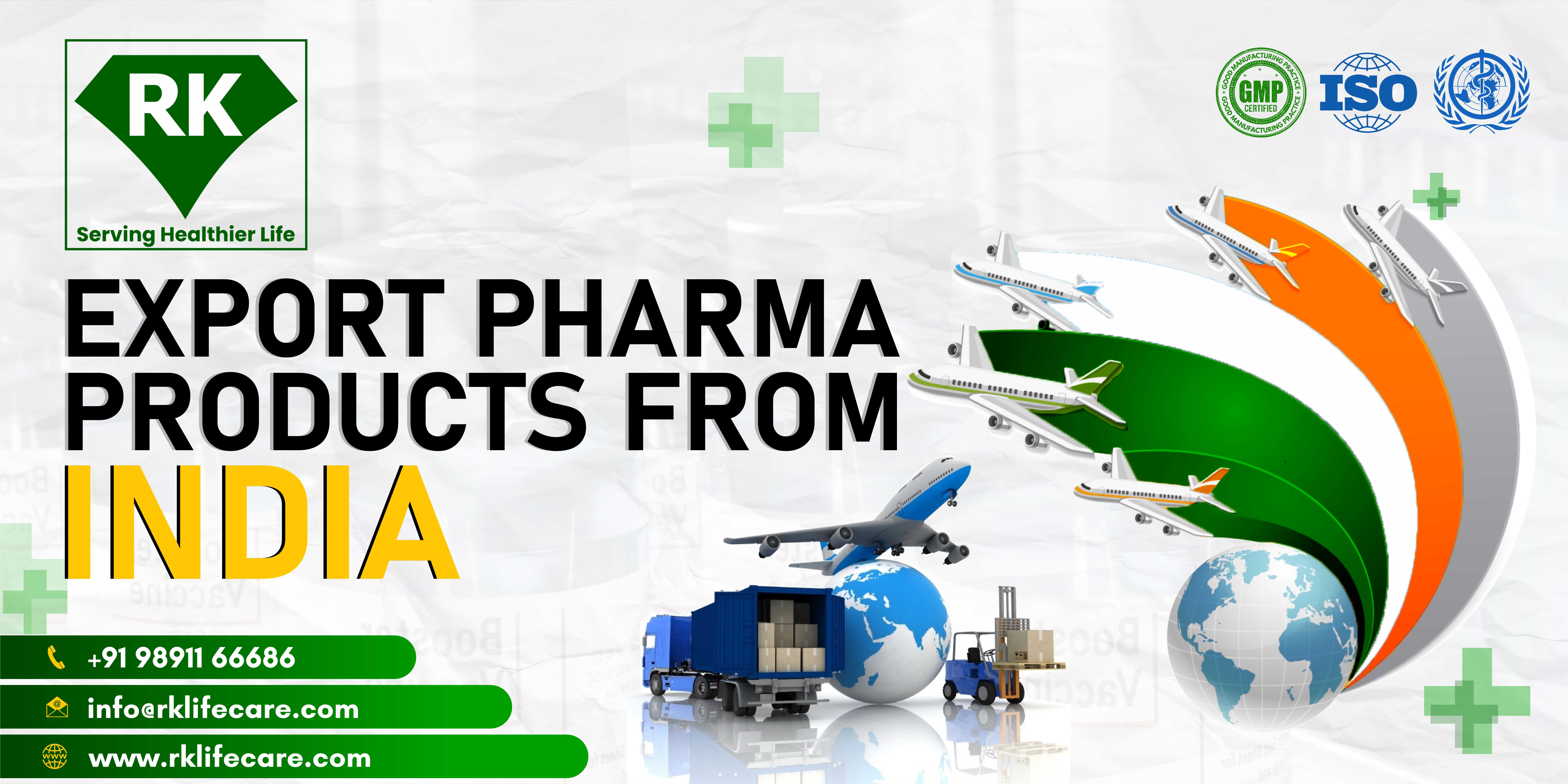
26 Feb 2025
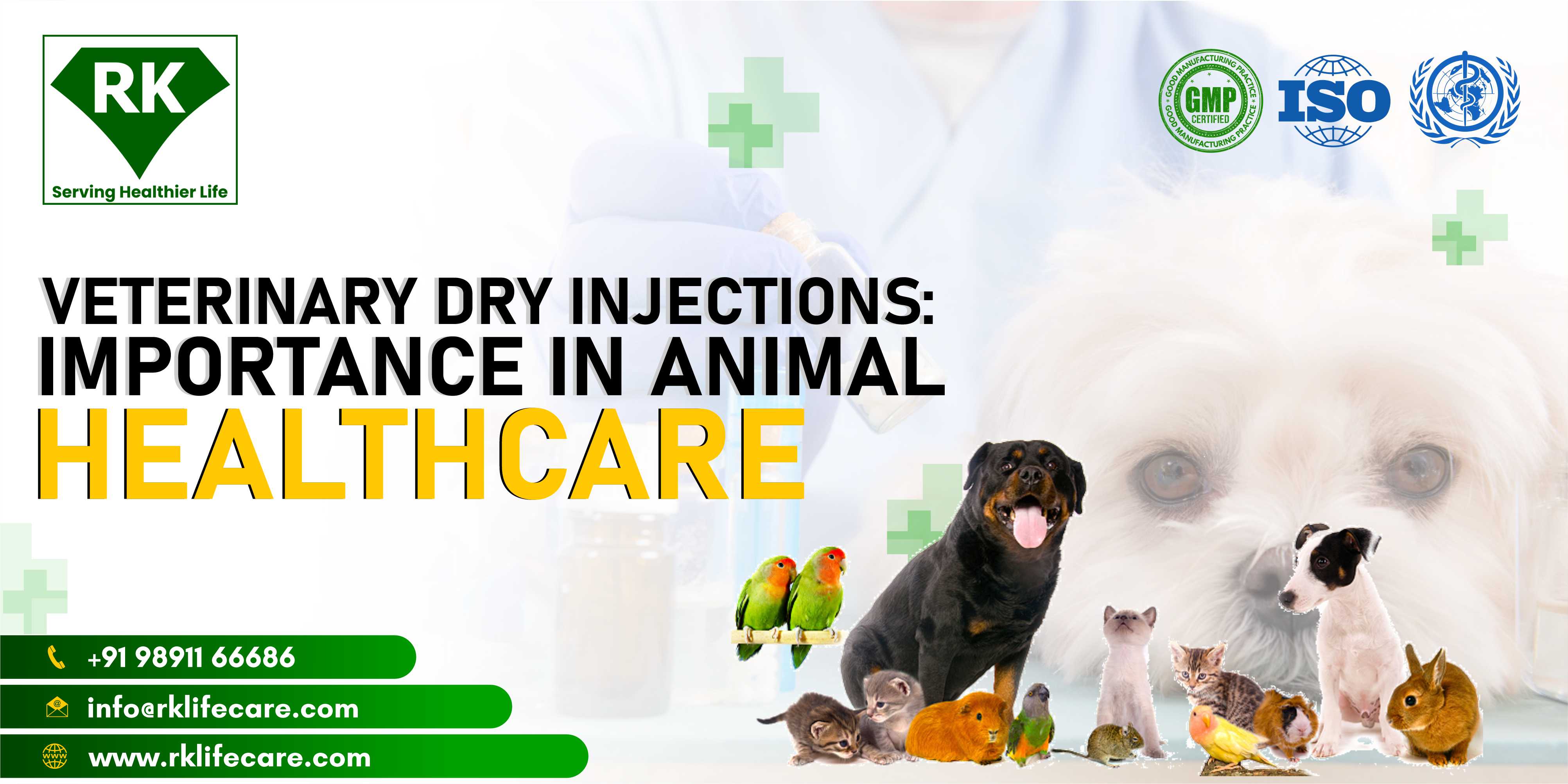
25 Feb 2025
.jpg)
24 Feb 2025
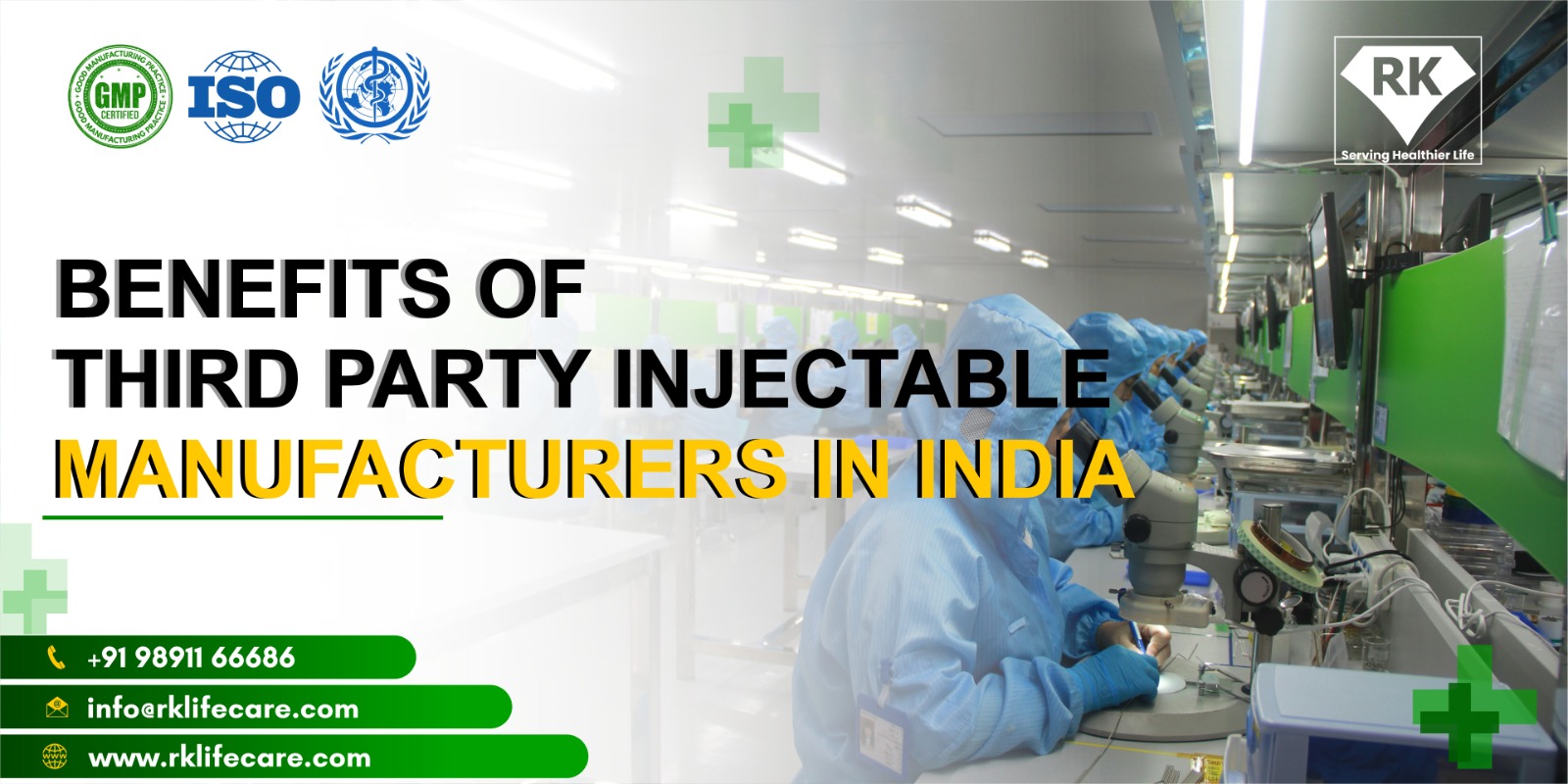
22 Feb 2025
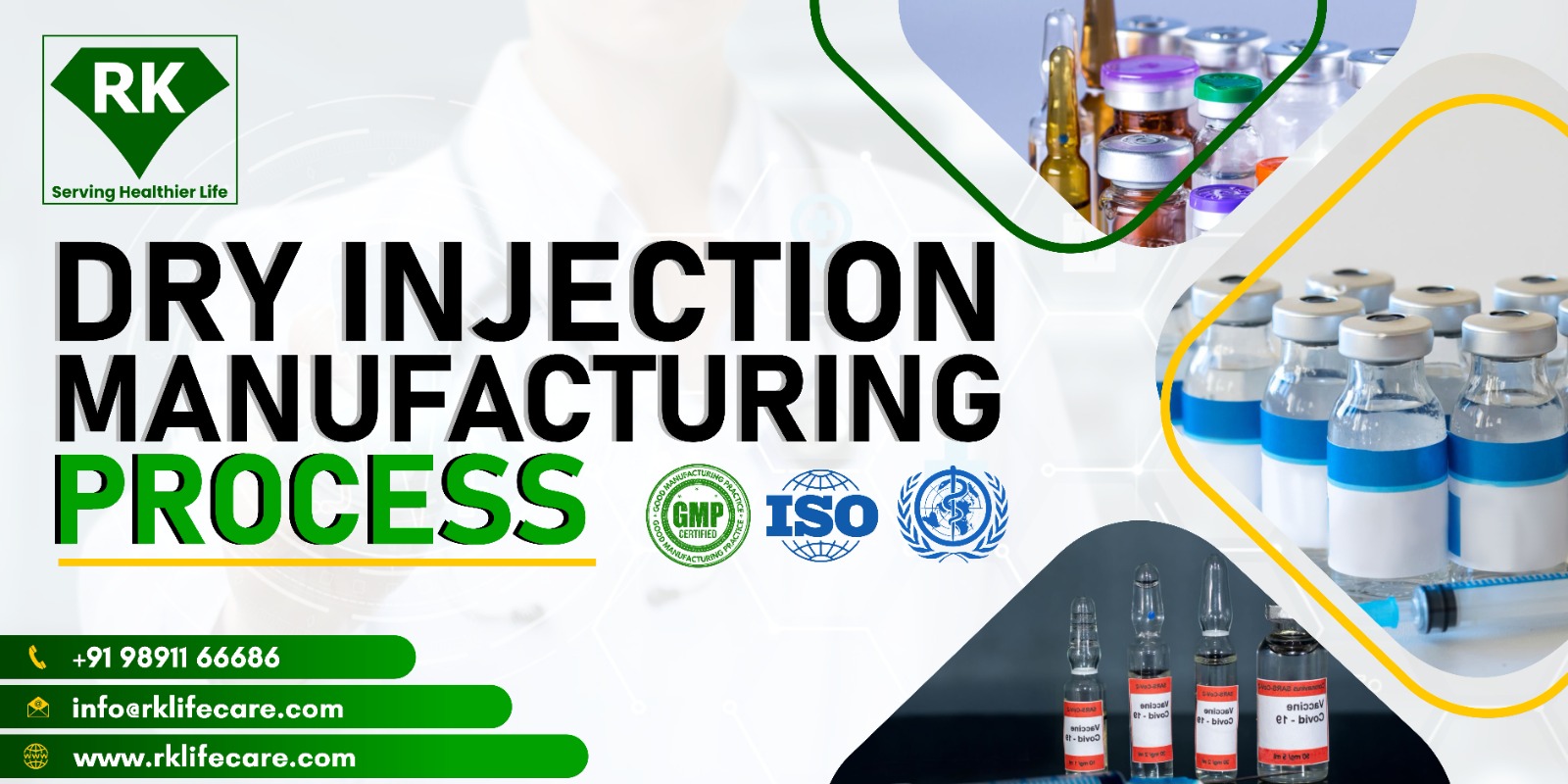
21 Feb 2025
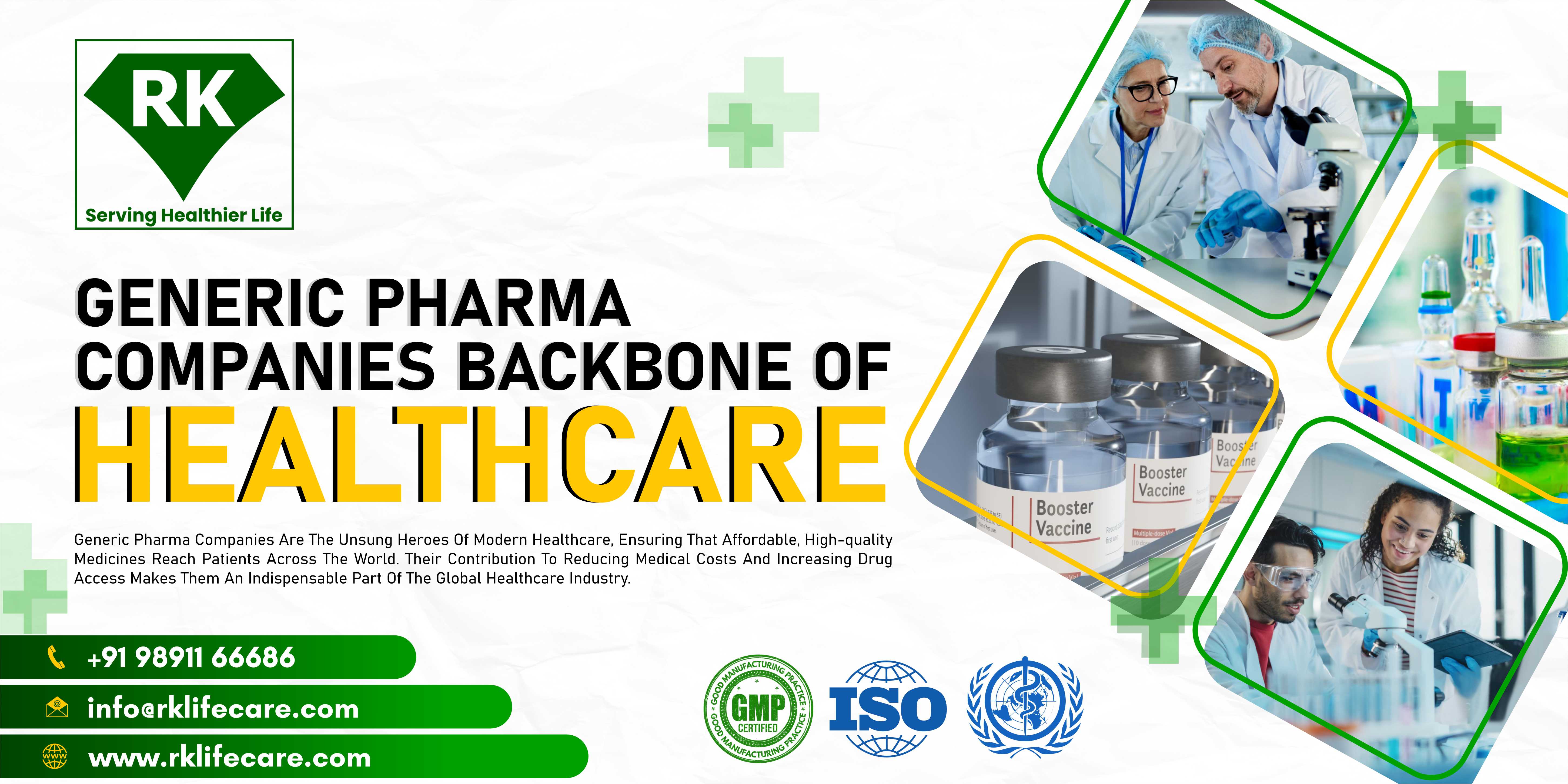
06 Feb 2025
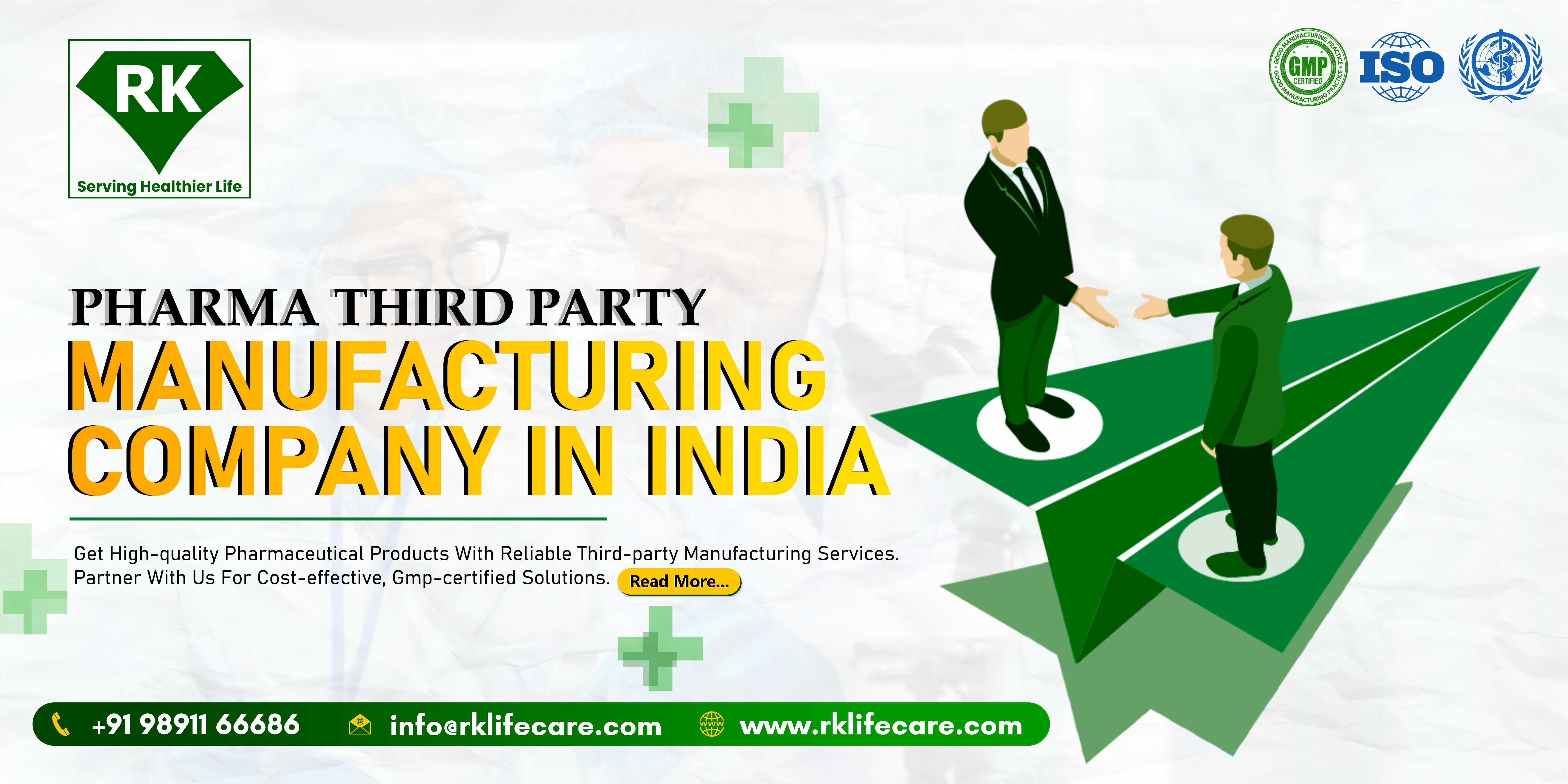
04 Feb 2025
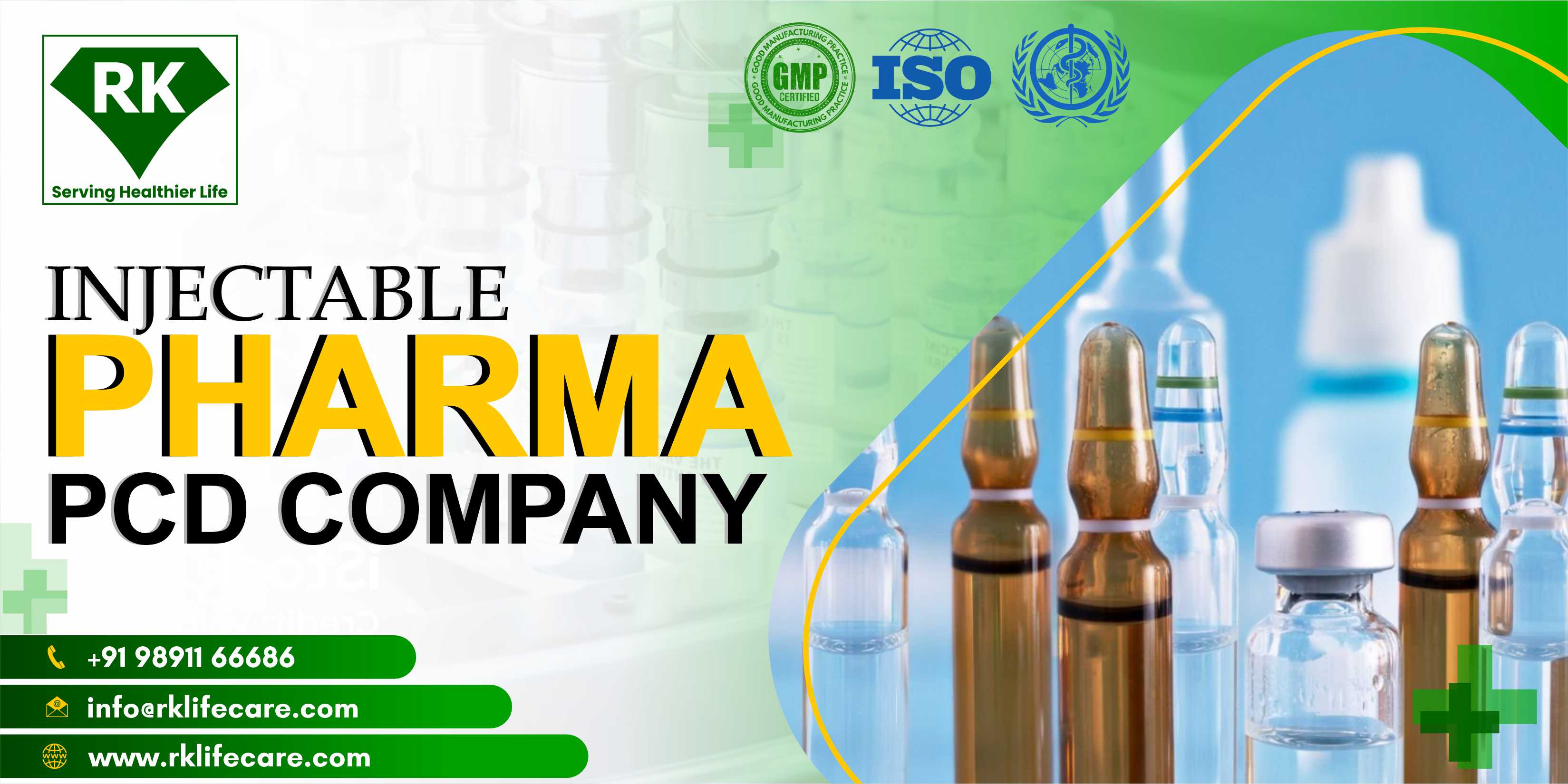
03 Feb 2025
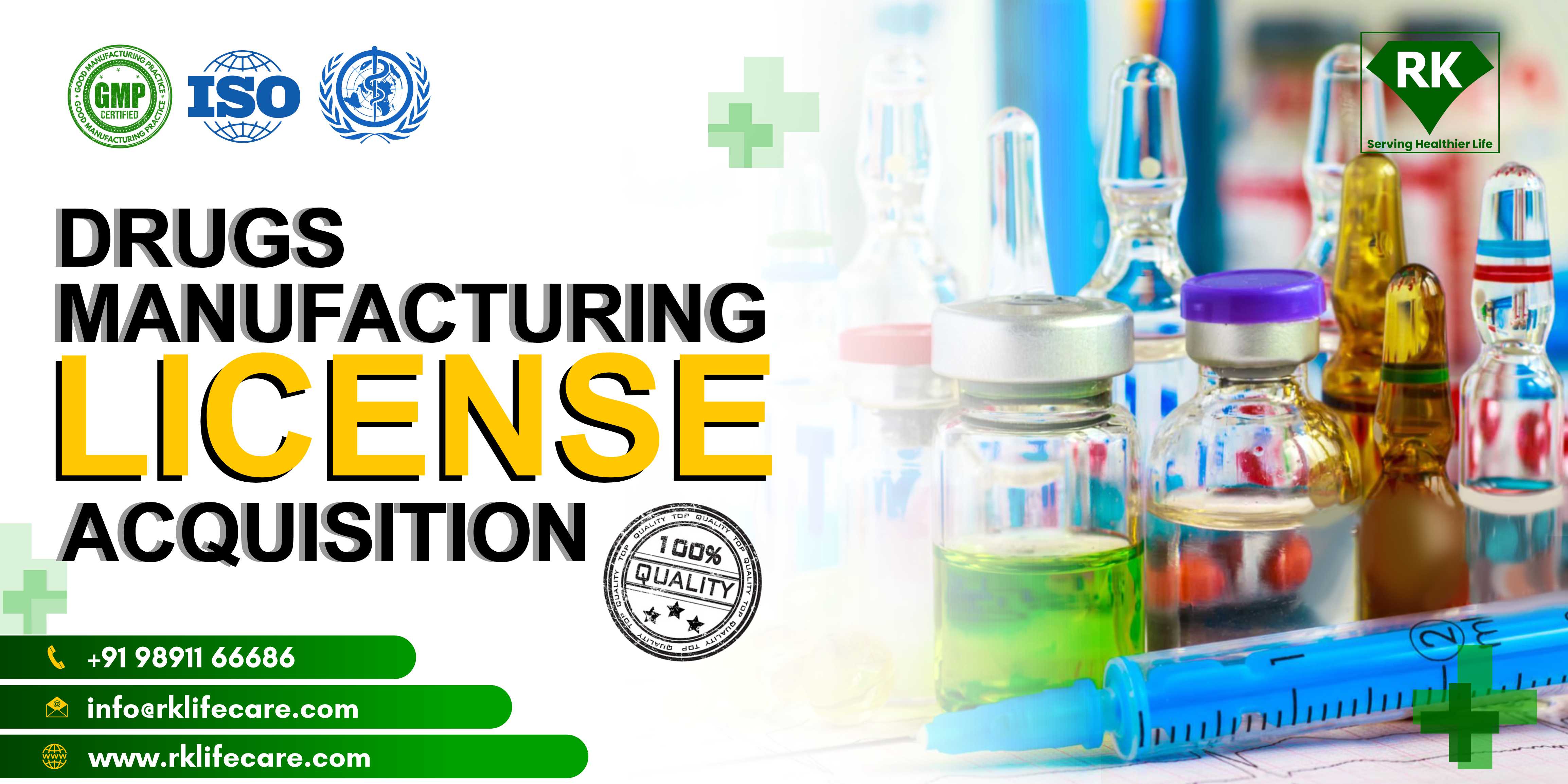
01 Feb 2025
.jpg)
29 Jan 2025
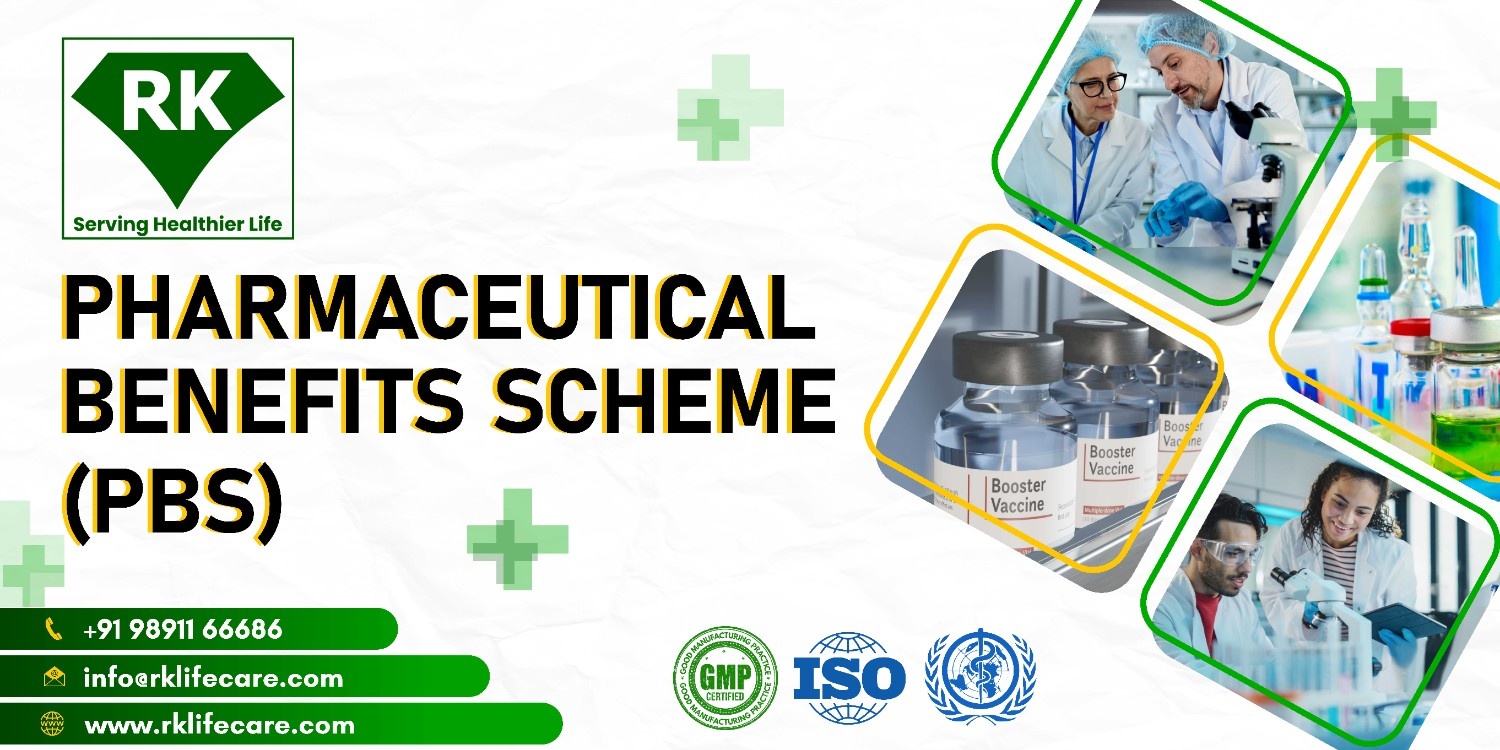
28 Jan 2025
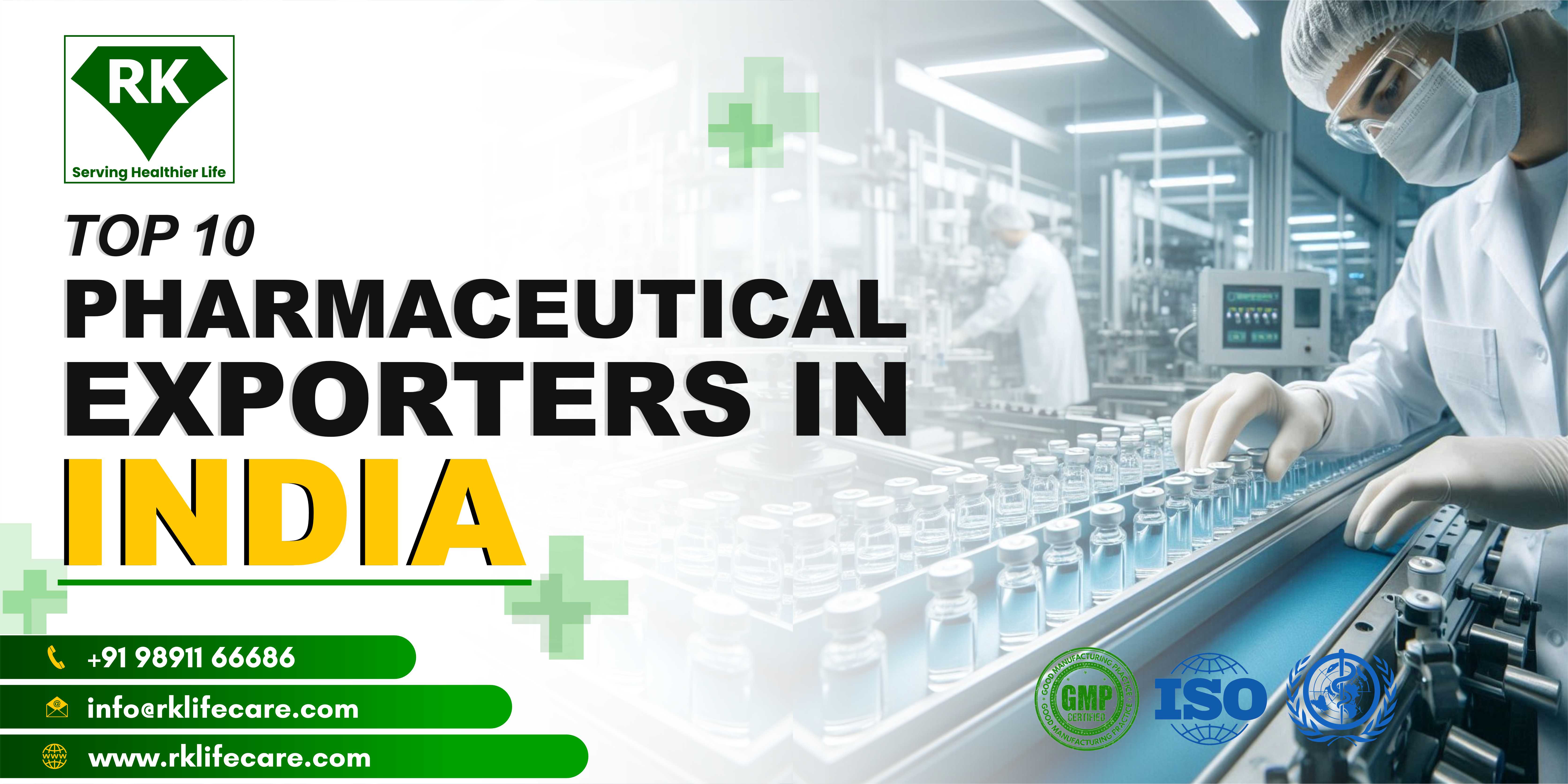
24 Jan 2025
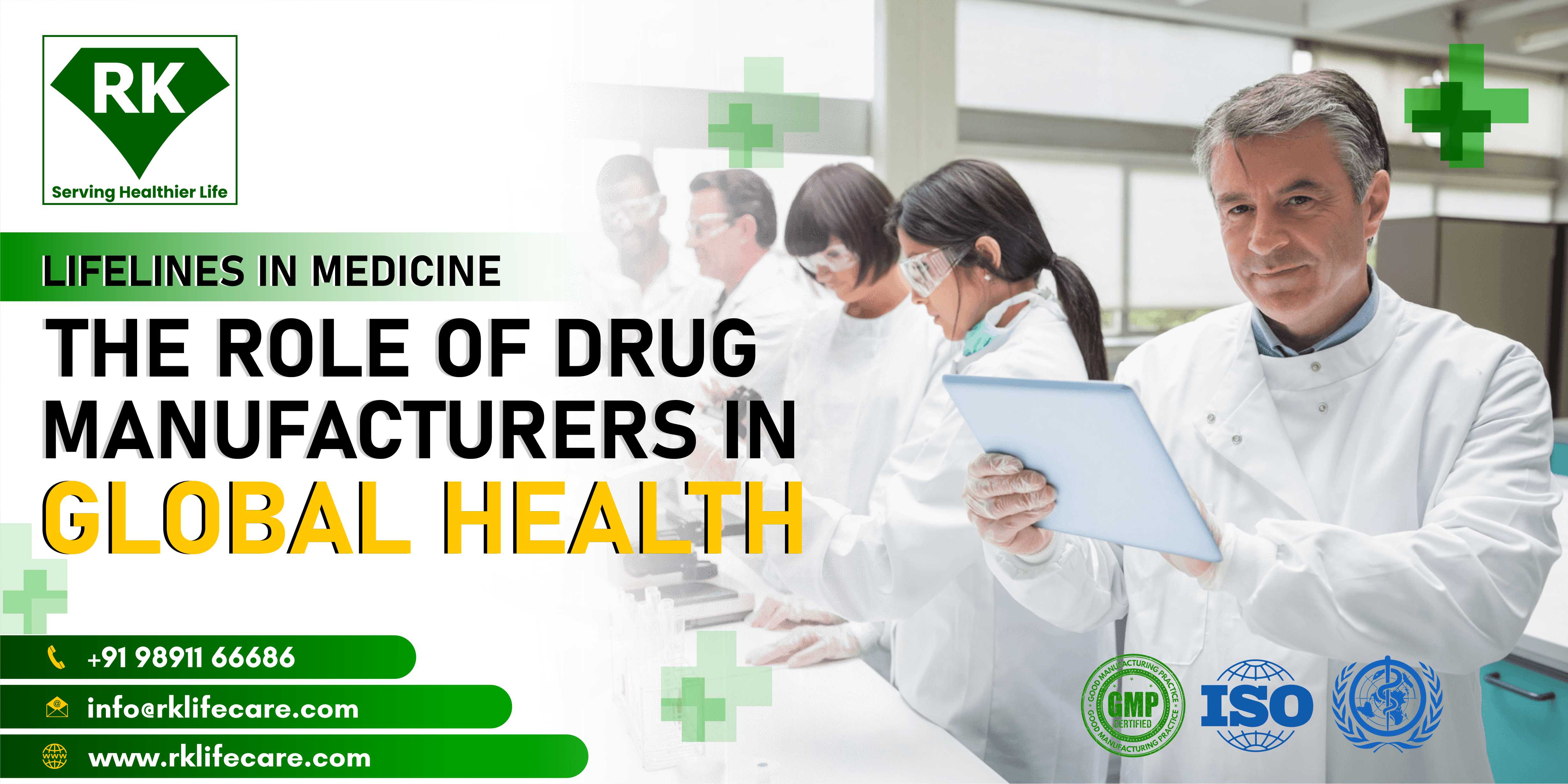
22 Jan 2025
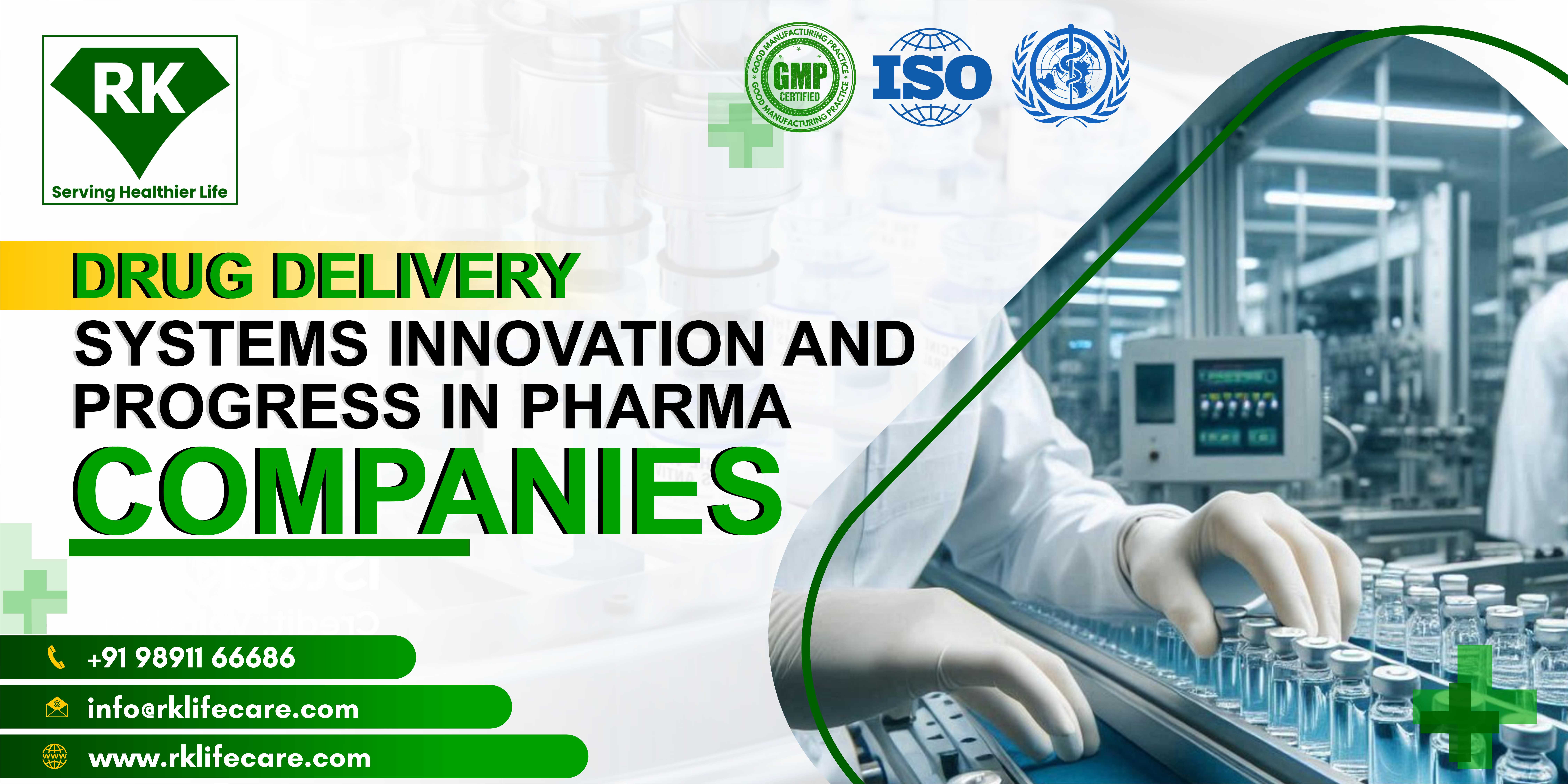
21 Jan 2025
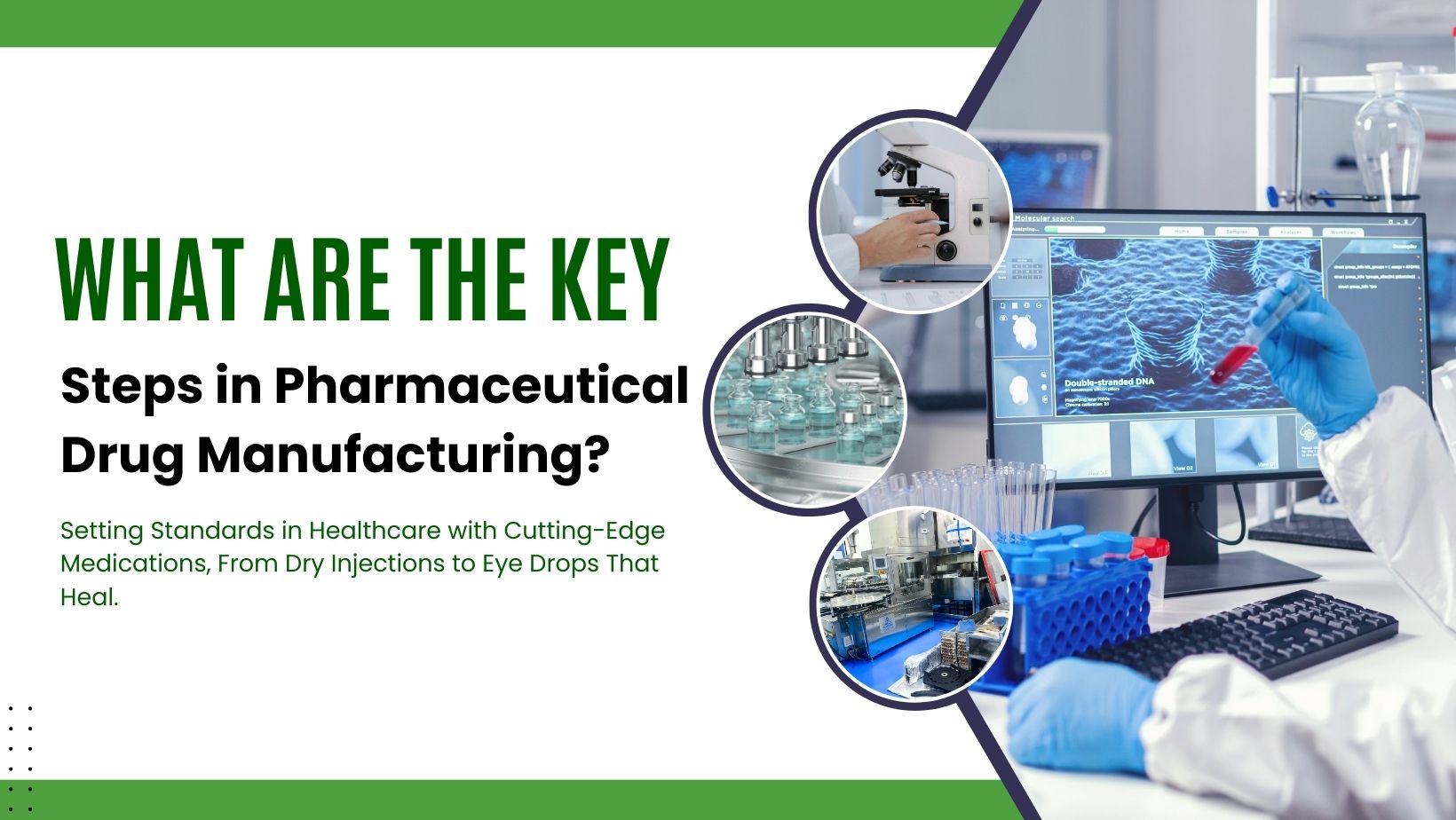
14 Jan 2025
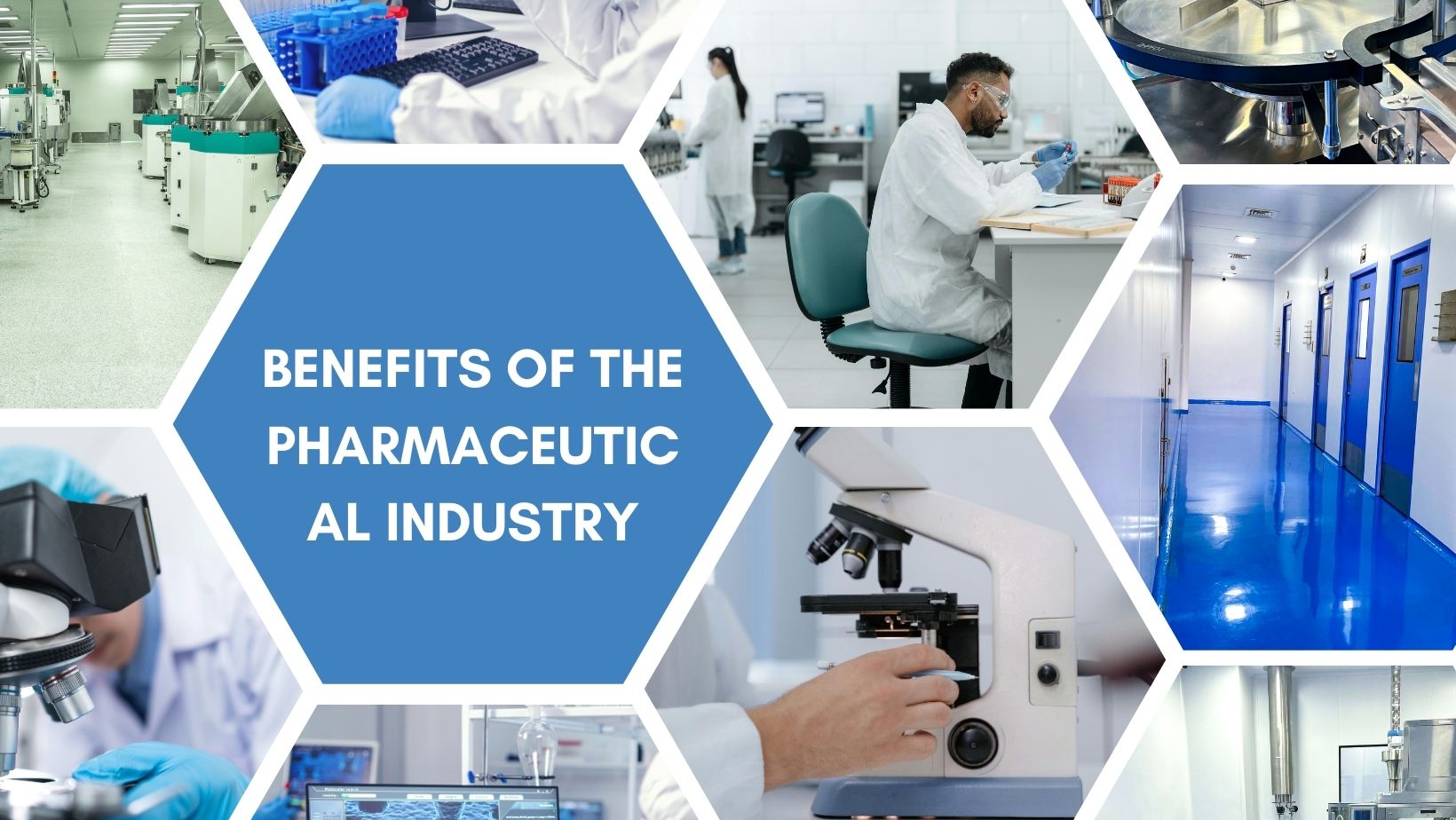
11 Jan 2025
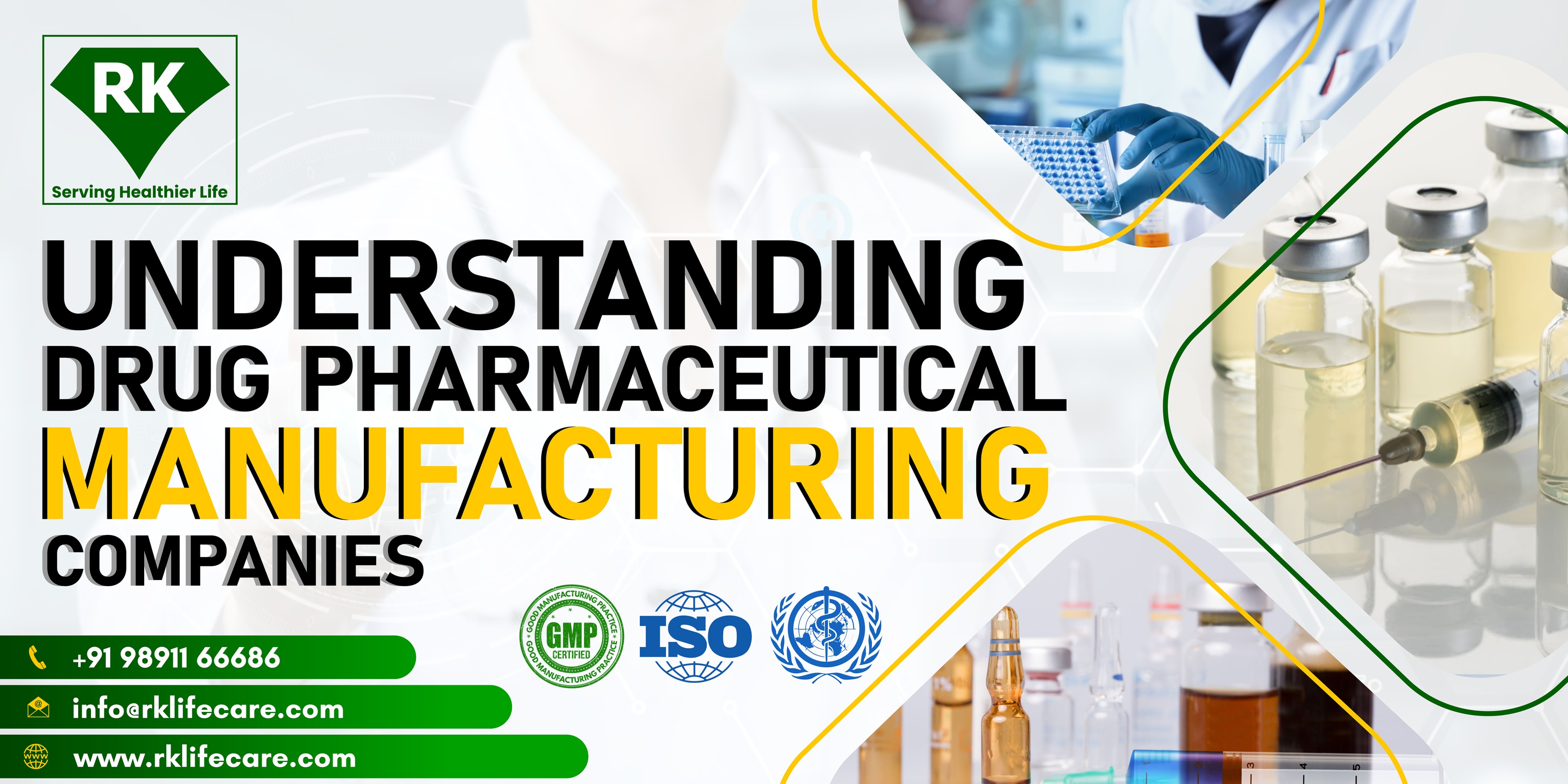
10 Jan 2025
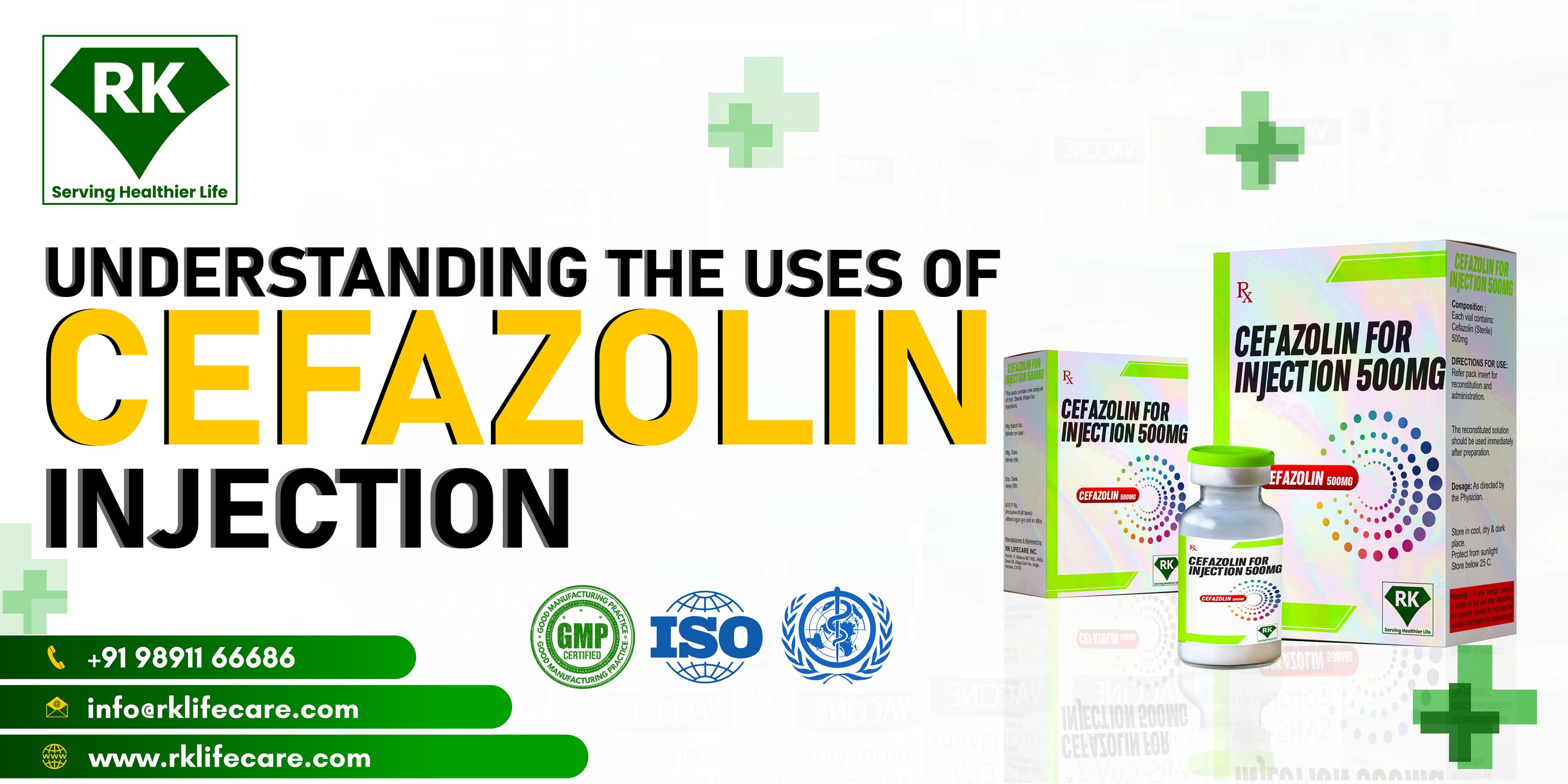
09 Jan 2025
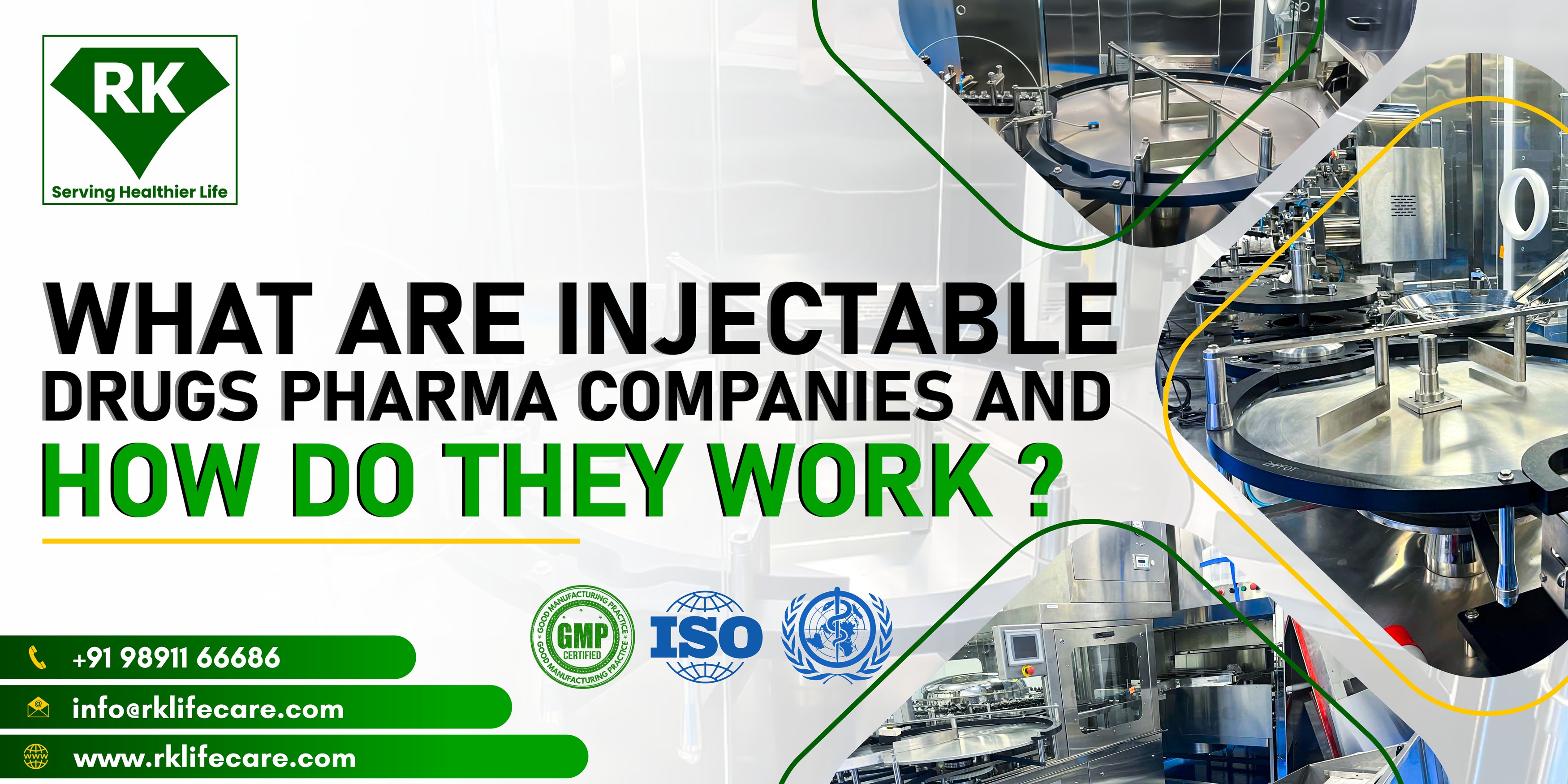
08 Jan 2025